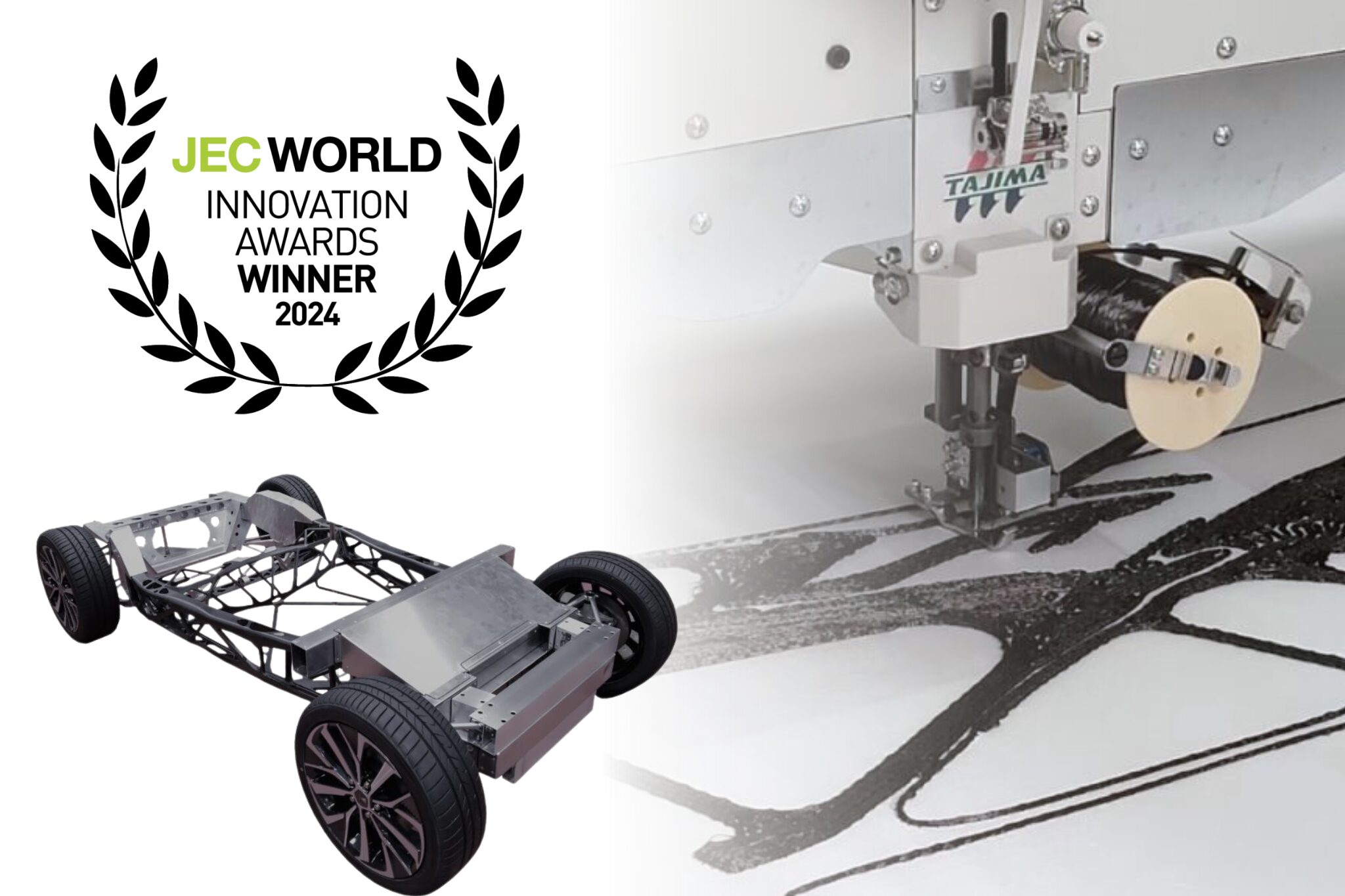
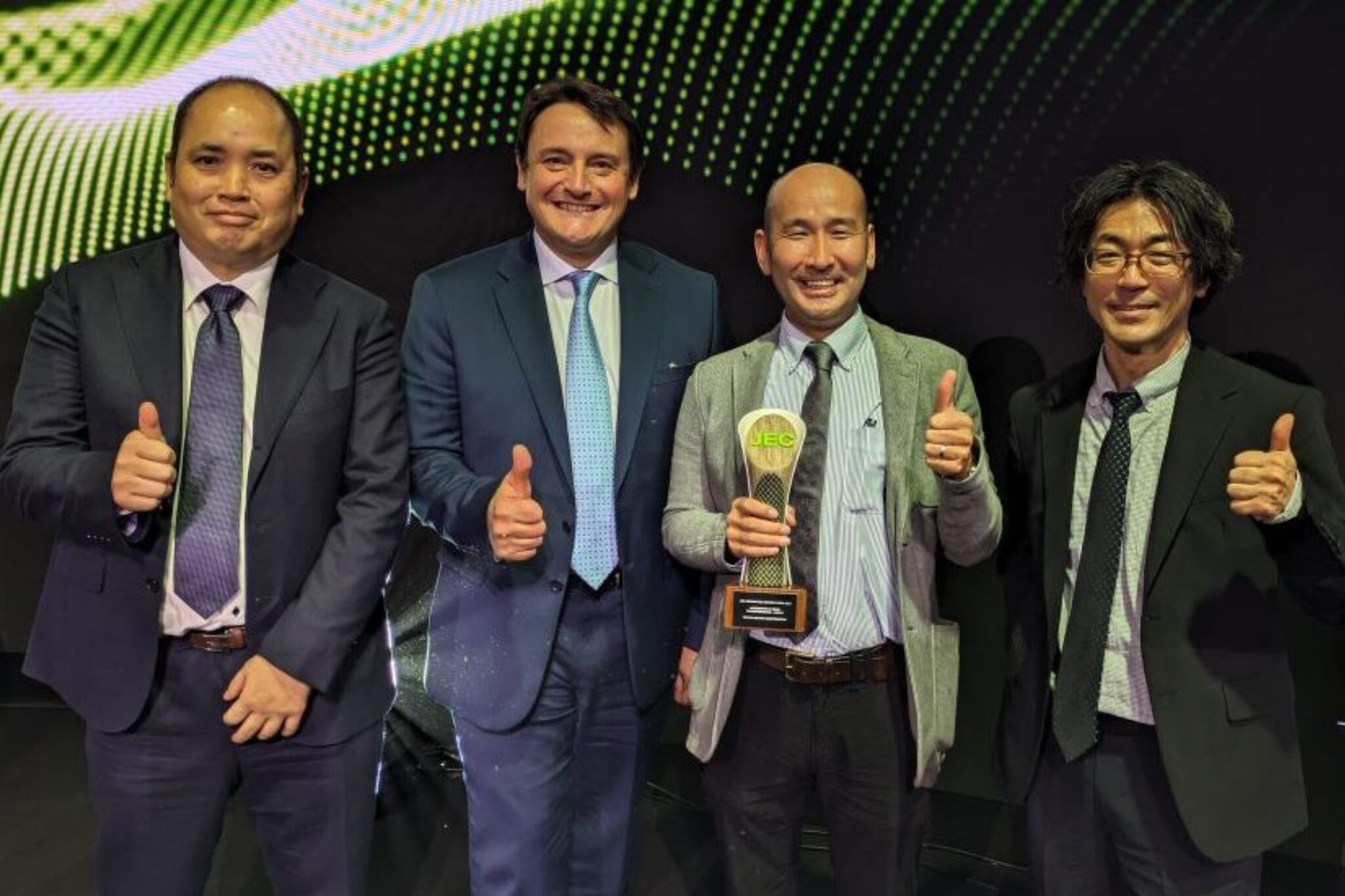
タジマグループの開発を担う株式会社 TISMが参画した「CFRP-アルミニウム一体型モノコック」の製作プロジェクトが、2024年2月に「JEC COMPOSITES INNOVATION AWARDS AUTOMOTIVE & ROAD TRANSPORTATION-PARTS 部門賞」を受賞しました。
このアワードは、フランスのJECグループが「複合材料の可能性を最大限に発揮する最先端の創造的なプロジェクト」を表彰する国際的な賞です。カーボンニュートラルに貢献する取り組みとしてCFRP(炭素繊維強化プラスチック)とアルミを複合した実物大の車両モノコックを製作する実証実験が、評価されました。4社※の協働によって進められたこのプロジェクトに、タジマの刺繍技術がどう活かされたのでしょうか。先端事業推進部の大橋にインタビューしました。
※トヨタ自動車株式会社、株式会社豊田中央研究所、株式会社トヨタカスタマイジング&ディベロップメント、株式会社TISM
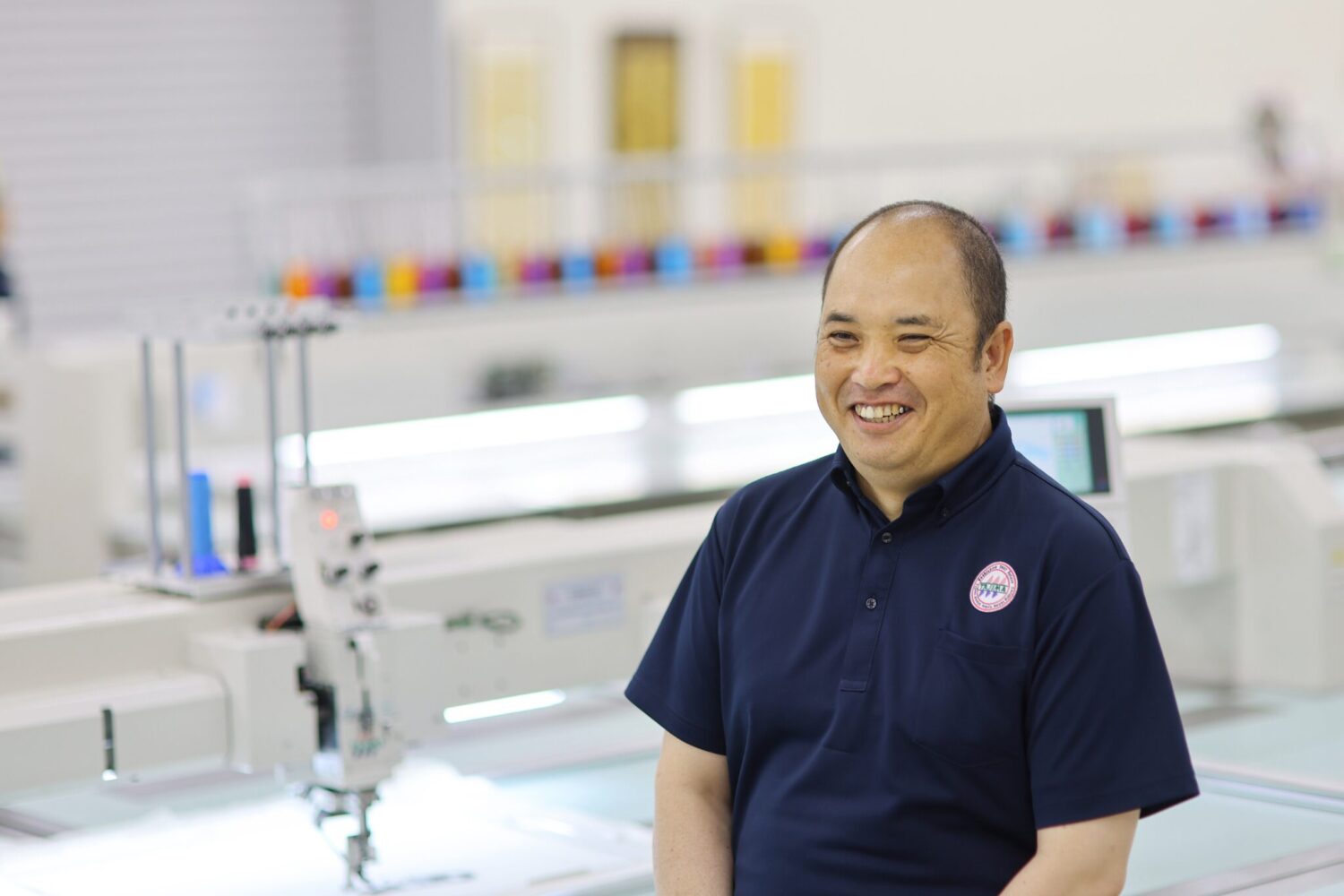
複合材料技術を評価する世界的な賞を受賞。自動車への技術展開で、刺繍の可能性を広げる。
株式会社TISM 先端事業推進部
大橋 功
TFP工法には大きな可能性がある
TISMを含む4社がこのプロジェクトで取り組んだのは、CFRPとアルミの一体化構造によって原寸大の車両モノコックを製作する実証実験である。CFRP部には、基材に強化繊維を縫いとめてプリフォーム(中間基材)を形成する、「TFP工法(テーラードファイバープレースメント工法)」という技術が使われた。タジマグループは、刺繍技術の応用を進める中でいち早くTFP工法に注目し、技術開発に取り組んできた。
その中でも、2015年頃から一貫してTFP工法の開発に携わってきたのが、先端事業推進部の大橋である。
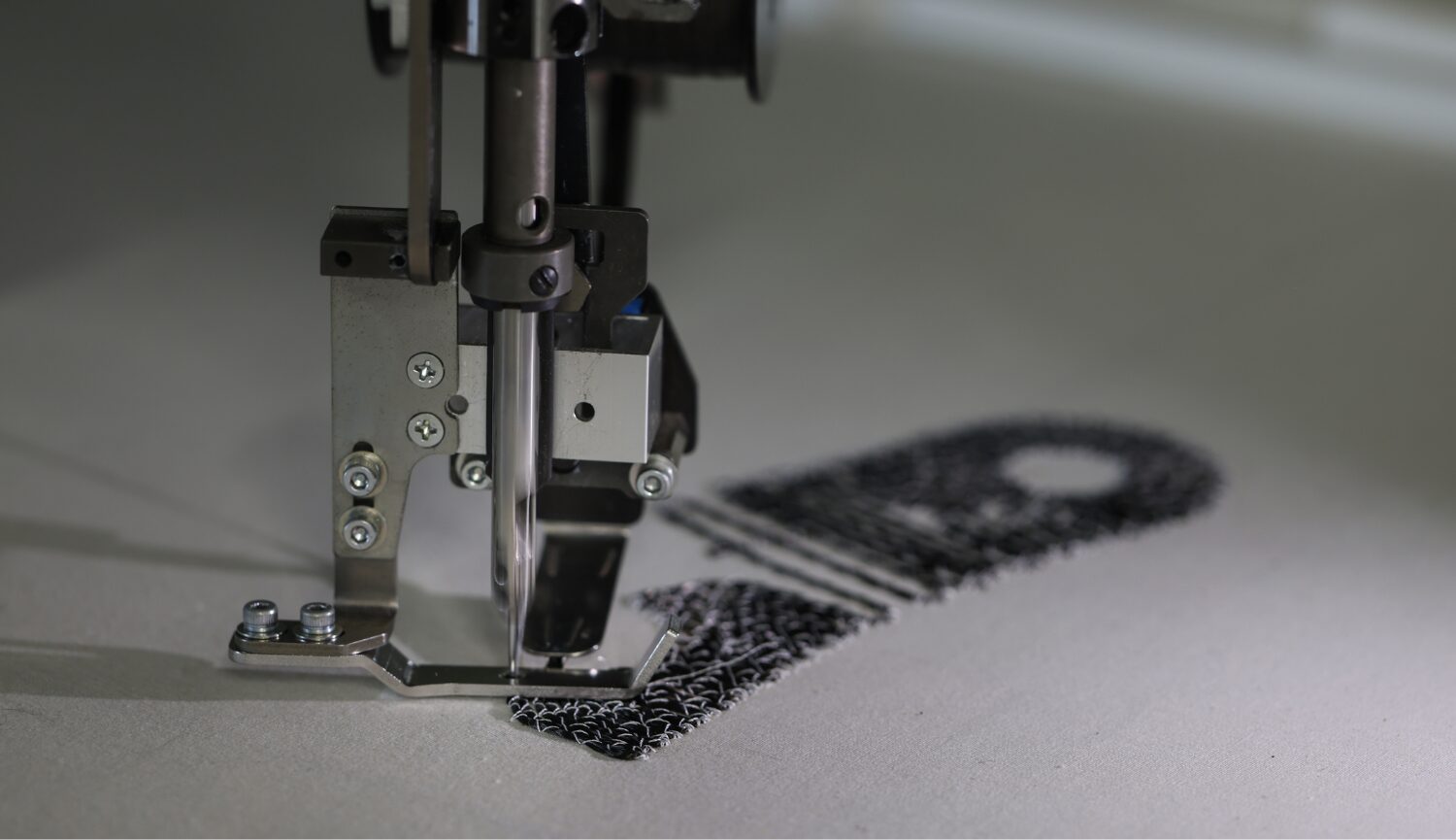

「私は入社当初、製造部でミシンの組み付けを担当していました。その後、開発部門に異動し、手がけることになったのがTFP工法です。当時の社長が、『TFP工法には大きな可能性がある。絶対に推し進めるべきだ』という強い思いを持っていて、メンバーを集め、その実現に向けて開発が始まりました」と振り返る。
CFRP部品を製造する際、従来はカーボンクロス(繊維を紡織した生地)による成形が一般的に行われてきた。しかし、CFRPは繊維長手方向のみ強度・剛性が高く、カーボンクロスによる成形はドーナツ型の中抜き形状や放射線形状など複雑な形状や繊維の向きには適していない。また、積層したシート材をカットする際に多くの端材が生まれ、材料の歩留まりの低さが課題となっていた。
そうした従来工法の課題をクリアするのがTFP工法だ。一直線だけでなく曲線を含め、さまざまな方向に強化繊維を配向することが可能で、強度を保ちながら複雑な形状を作り出すことができる。また、繊維を切断することなく最小限の材料で配向できるので、材料の廃棄を大幅に減らすことができる。まさに、CFRPの可能性を最大限に引き出せる工法といえるのだ。
TFP工法の詳細はこちら
実物大の車両モノコックを作る
ただし、TFP工法の開発が決して順風満帆だったわけではない。特に、繊維を最適な位置に縫いとめる技術は難易度が高く、導入には長い道のりがあった。最適な繊維配向を実現するために力を入れたのが、刺繍機の改良や新たな制御システムの開発である。
そうしたさまざまな試行錯誤が実を結び、2009年に強化繊維の縫い付けに特化した刺繍加工機「TCWM」が誕生した。TCWMの大きな特長は、コンピュータ制御された縫い付けヘッドで正確に強化繊維を縫い止められることだ。縫い付け角度を0°~360°まで自在に調節し、完成品の形状に合わせて繊維を配向することができる。
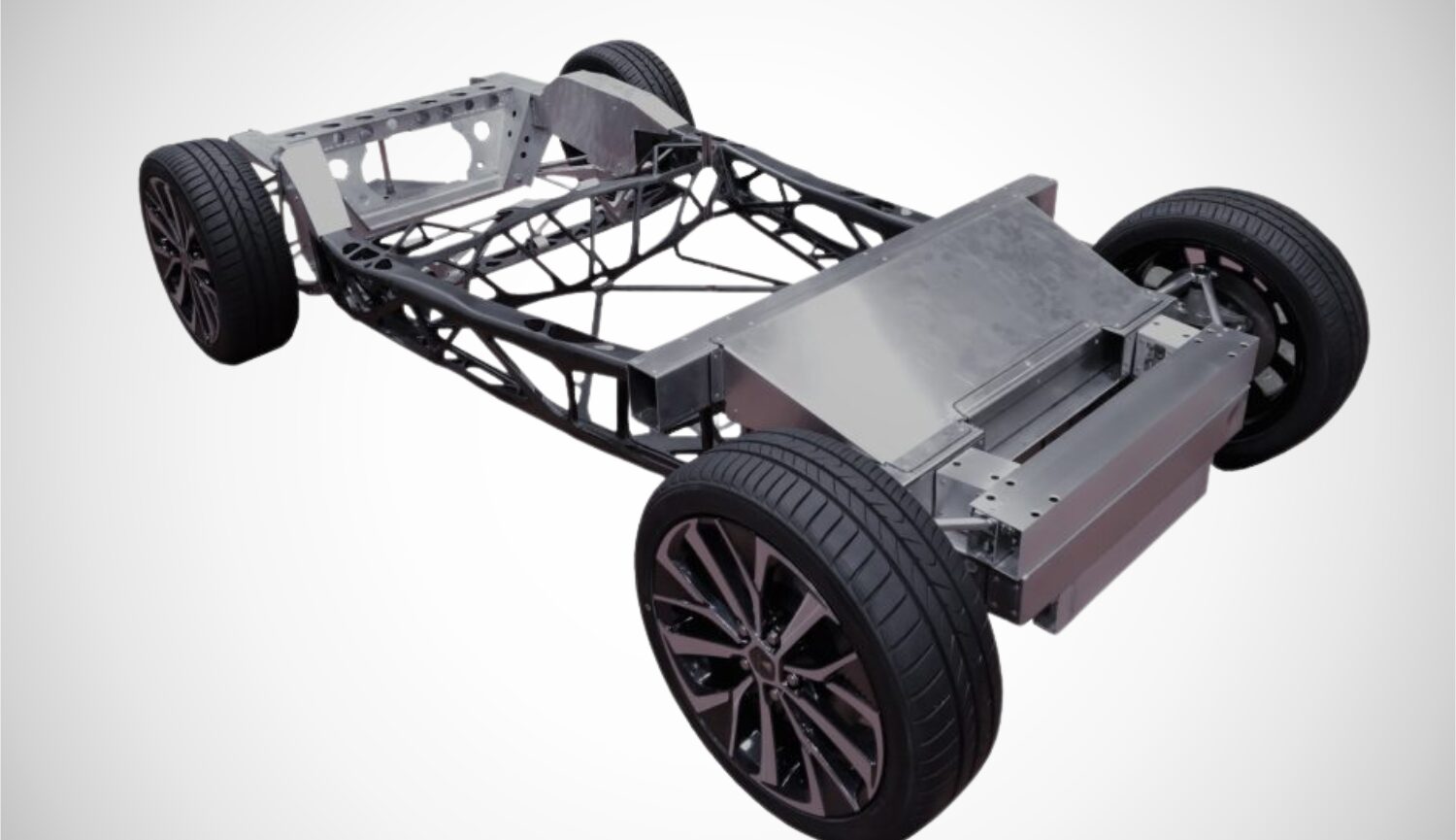
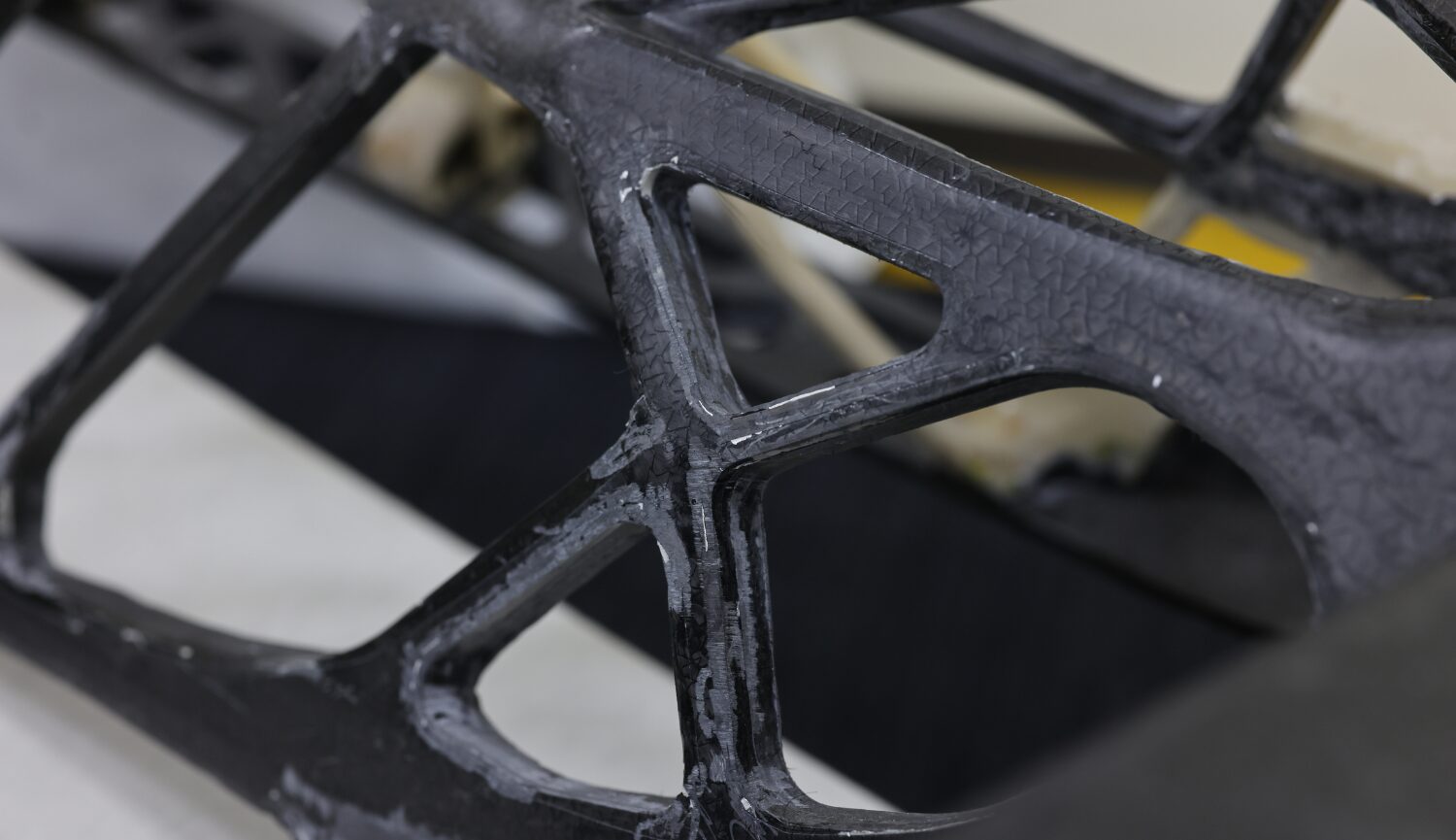
トヨタ自動車との共同研究では、車両のウイング部分の軽量化をめざすプロジェクトが進行。オリジナルはアルミ製で質量は425gあったものがTFP工法では119gとなり、72%の質量低減に対し、オリジナルと同等の剛性の確保に成功した。「車両を軽量化できると燃費が向上するので、結果としてCO2の排出量を減らすことができます。そうしたものづくりに活用できるのがTFP工法です。カーボンニュートラルに貢献する技術だと、胸を張って言うことができます」
そして、着実に蓄積した技術の集大成として取り組むことになったのが、受賞した実物大の車両モノコックの製作である。
「今まで取り組んできた小さいサイズの製作にも相当な時間がかかったので、実物大の車両モノコックを作ると聞いた時はとても驚きました。いろんな企業が関わる中で、当社に求められる役割をしっかりと果たす必要があります。そのプレッシャーは大きく、『本当にできるのか?』と自問自答していました」と、大橋は当時の心境を語る。
カーボンニュートラルに貢献するものづくり
TFP工法では、必要な方向に強度を持たせるための適切な繊維配向が必要になる。車体の各部位への力のかかり方を解析し、繊維の配向が行われた。一台の車両モノコックを構成するパーツの数は約70。大橋たちTISMの開発チームは、そのパーツ一つひとつにCFRPを正確に縫いとめていった。「繊維(強化繊維、炭素繊維)を縫う際は3Dモデルを平面展開した図面を使うため、曲面の部分などに多少の誤差が出ることがあります。また、刺繍をする時はどうしても生地が縮みます。その誤差を考慮し、ずれを調整しながら形にしていく難しさがありました」
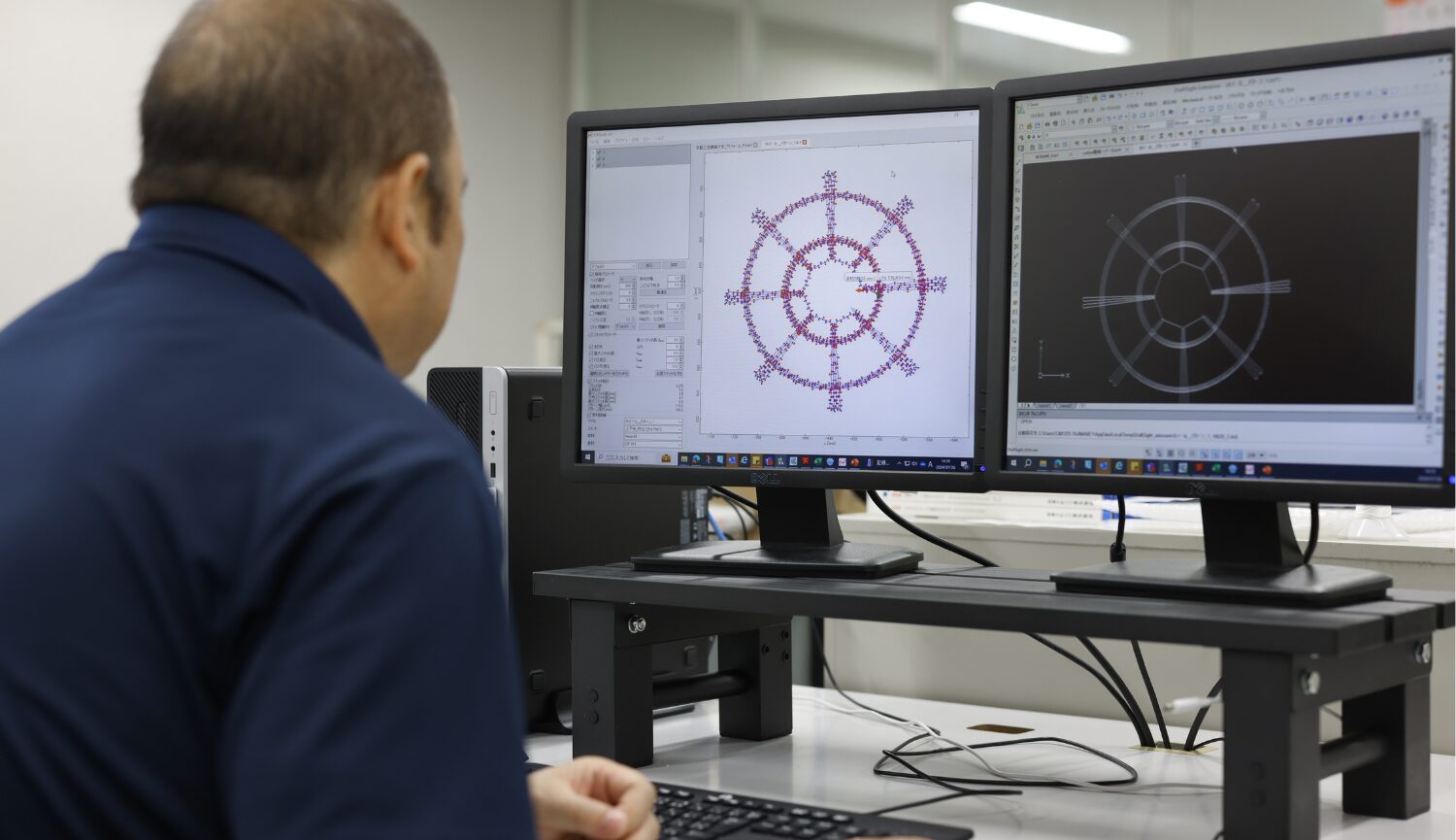
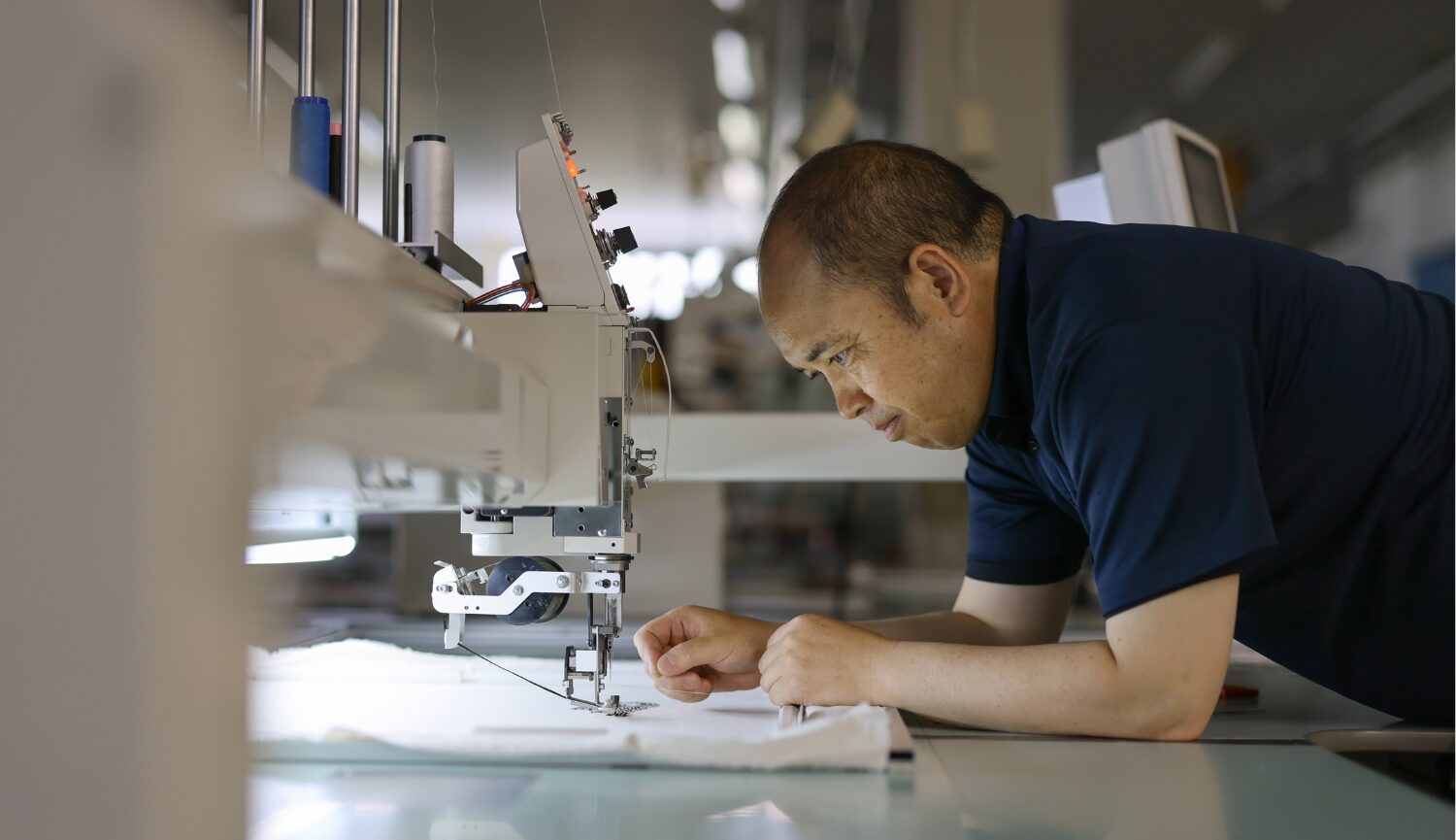
今まで誰も経験したことのないものづくりへの挑戦。
4社それぞれの強みを発揮しながら一つひとつの課題をクリアし、CFRPとアルミを複合した実物大の車両モノコックが、構想から2年の時を経て完成した。CFRPを効果的に使用した結果、参照設計45kgに対して15%の軽量化を実現し、繊維材の廃棄率を4%まで抑えることに成功。カーボンニュートラルに貢献するものづくりが認められ、「JEC COMPOSITES INNOVATION AWARDS」の受賞が実現した。タジマが培ってきた刺繍技術が、自動車という新しい領域に活かされ、社会課題の解決につながる取り組みとして実を結んだのである。
「TFP工法の開発に取り組み始めて以来、当社の中でも多くの人たちが苦労を重ねながら技術を開発してきました。その思いがつながった結果だと思います。素晴らしい賞を受賞することができ、本当にうれしく思っています」
タジマは今、TFP工法のさらなる可能性を探究し、航空機やモビリティ分野など新たな分野への展開を模索している。
持続可能な社会の実現に向けた挑戦を、技術の進化を担う者たちがさらに加速させていく。
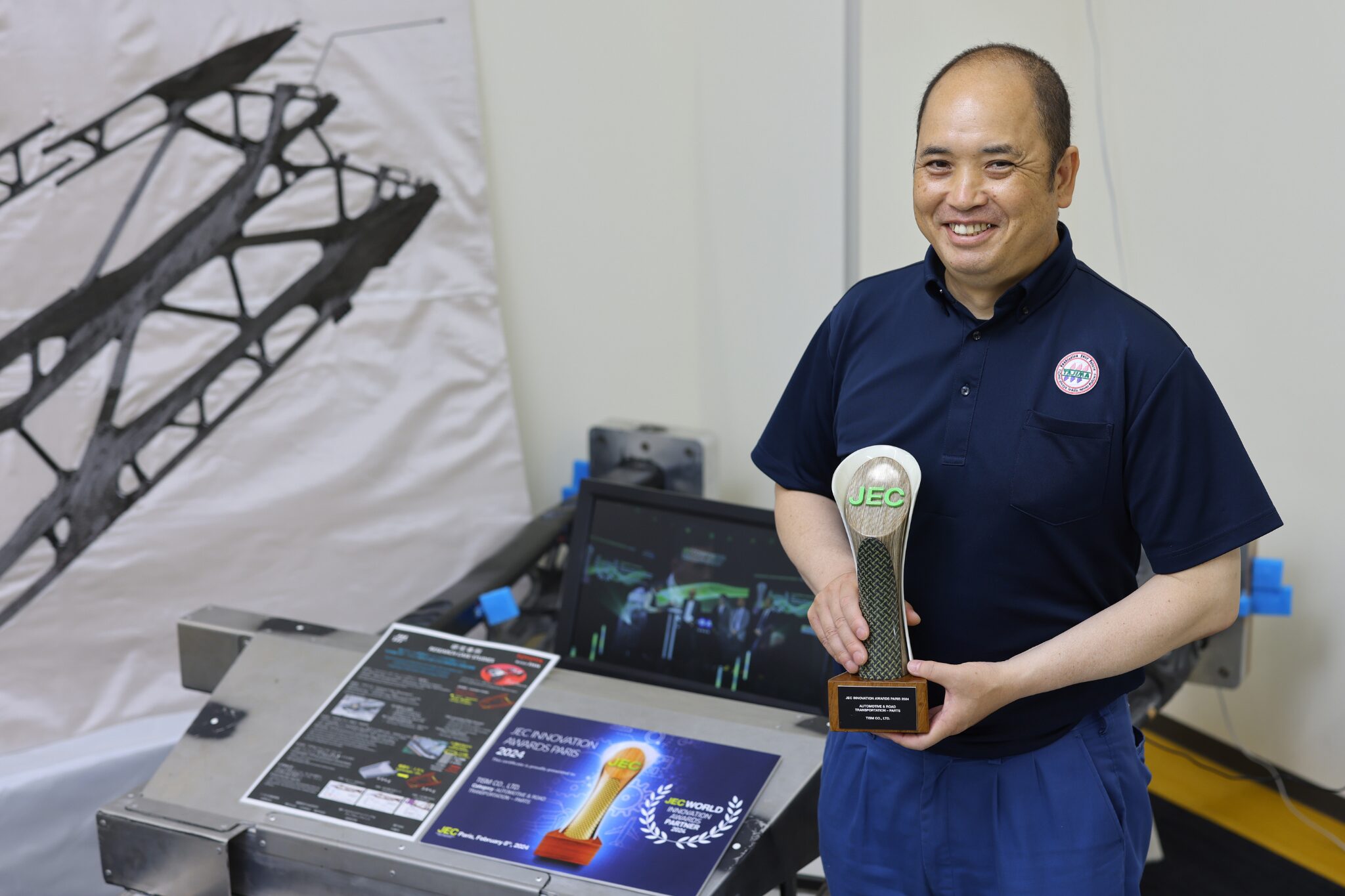
▶Click here to see the press release about JEC COMPOSITES INNOVATION AWARDS.