Tajima’s technology responds flexibly to social transformation
“Even in an environment without skilled operators, it is possible to produce exquisite and beautiful embroidery.” Due to the aging population and changing lifestyles, it is difficult to find skilled professionals in the embroidery industry at production sites. To solve this problem, Tajima developed the AI technology “i-TM” and DCP.
In addition, as the personalization business is gaining momentum due to diversifying tastes, embroidery personalization is also attracting attention. Tajima’s technology supports such new business trends. With “i-TM + DCP”, we can provide embroidery processing tailored to your needs easily and with high quality.
What is “i-TM + DCP” ?
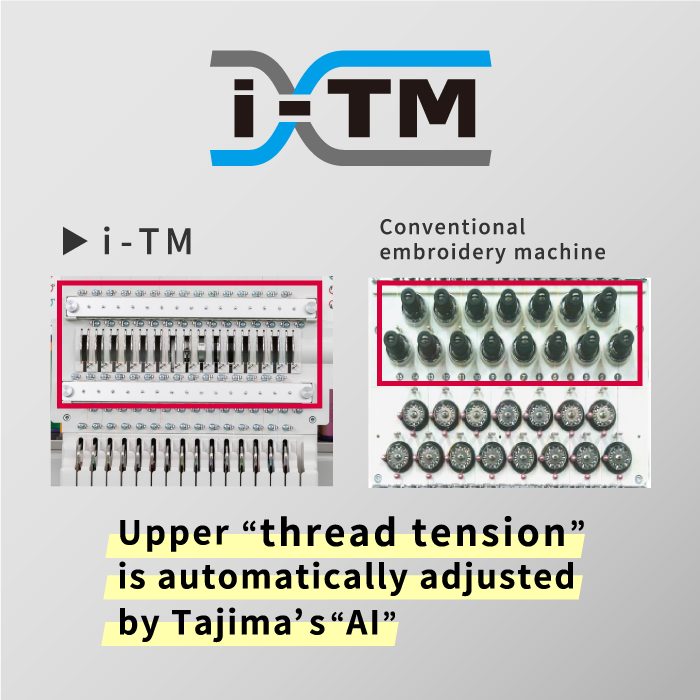
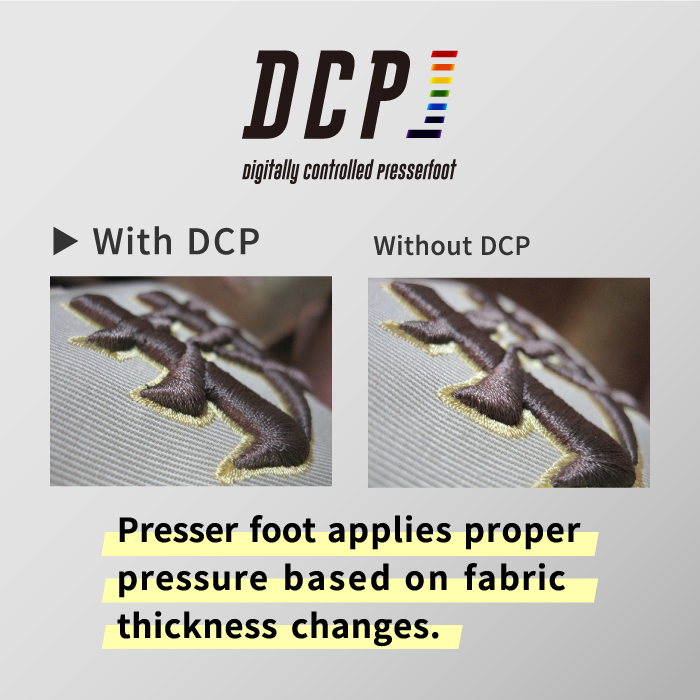
Approach to optimal stitching
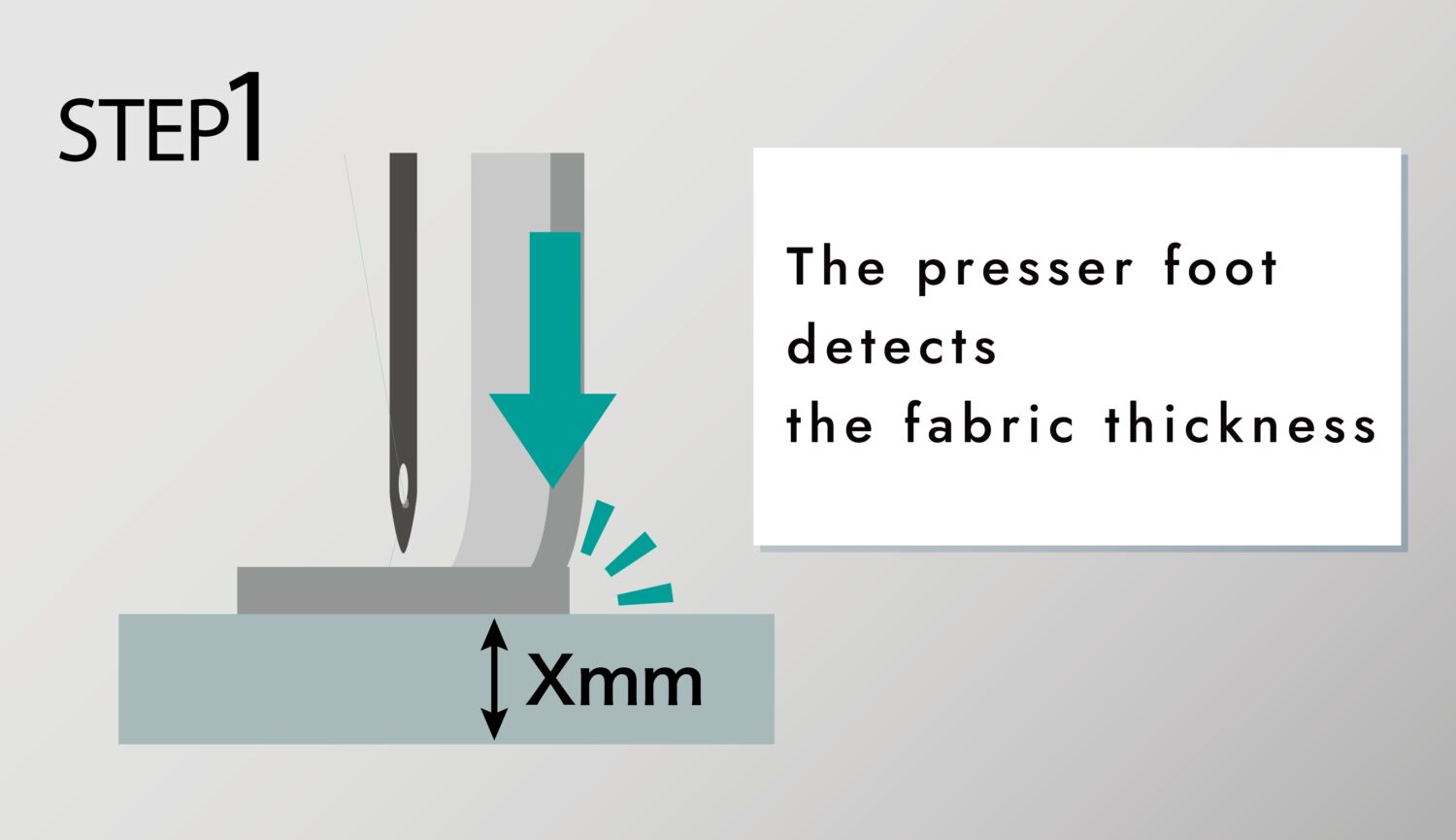
STEP1: DCP measures fabric thickness instantly
Measures fabric thickness in as little as 0.05 seconds per stitch.
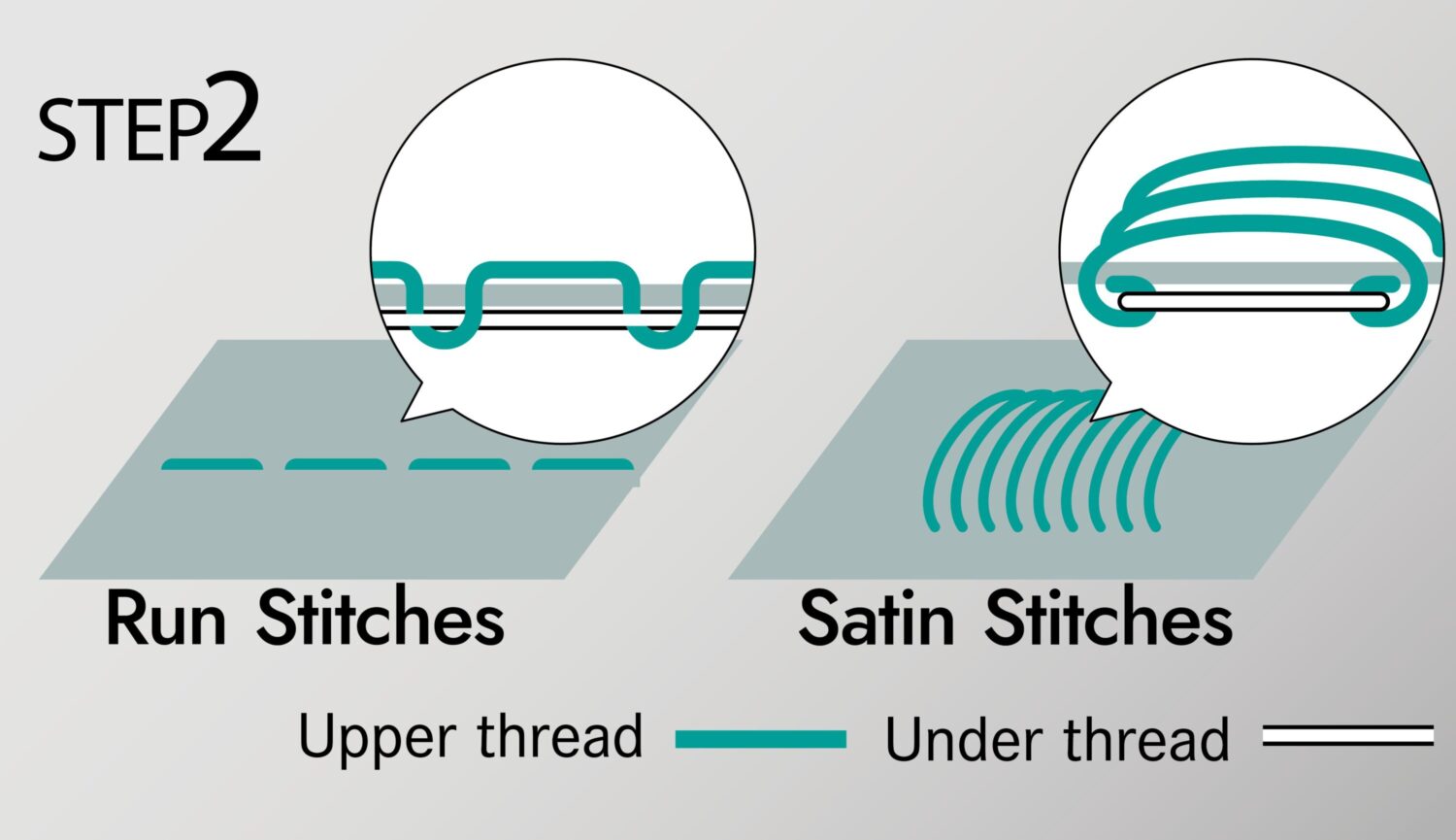
STEP2: i-TM identifies stitch types
Determines stitch differences by looking at design data.
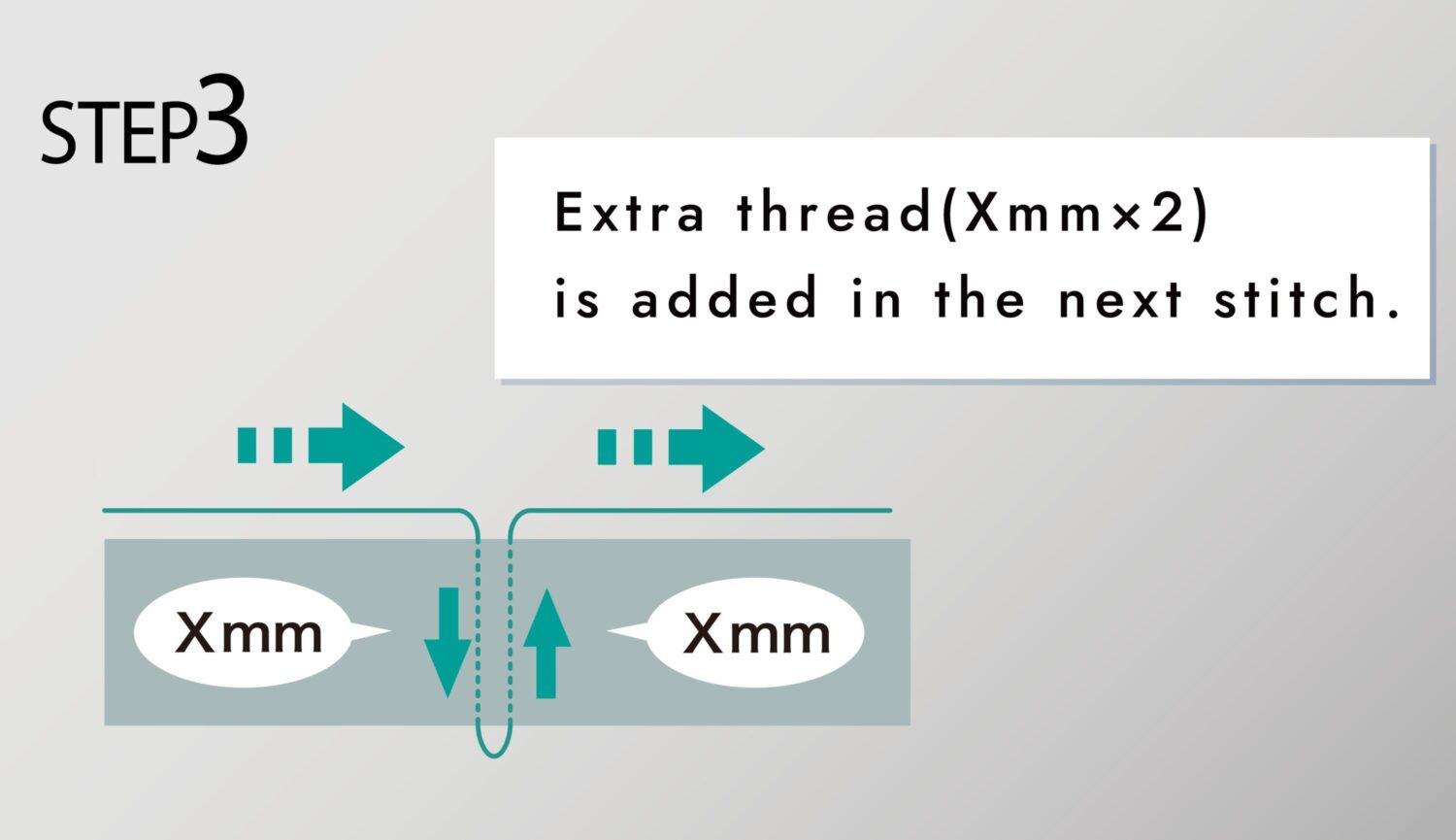
STEP3: Automatically supplies optimum upper thread volume
Automatically supplies the required amount of upper thread, calculated based on fabric thickness and stitch differences.
Value provided by “i-TM + DCP”
High Quality
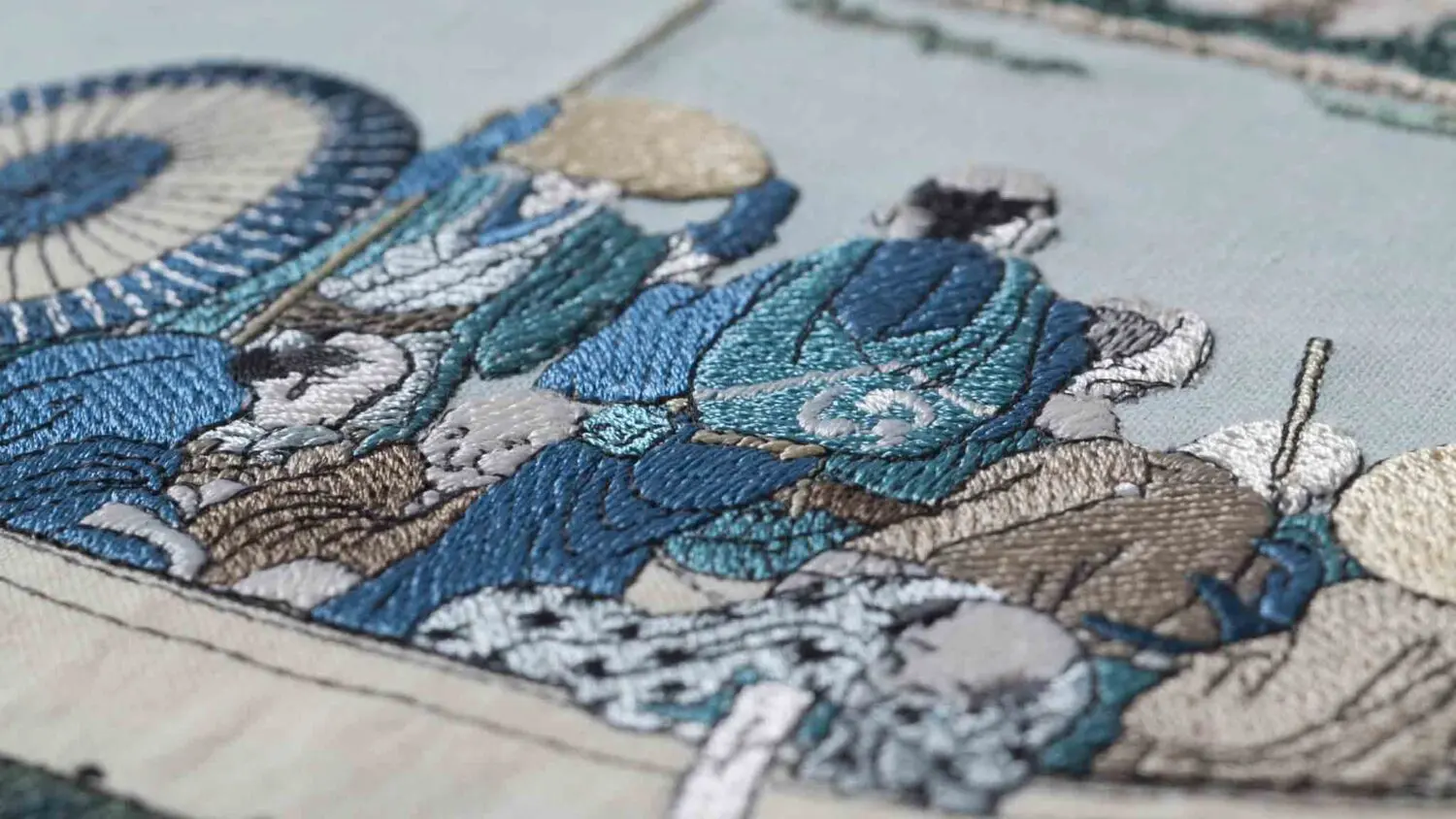
Quality indifferent of material and stitch type
Optimal upper thread supply, unaffected by material or design, results in high quality embroidery at all times. Even materials that are difficult to adjust for, such as thin summer fabrics in particular, can be finished beautifully. The DCP sensor also allows the upper thread volume to be changed even for items that are thicker in one part, such as hoodies. No need to change embroidery machine settings when changing to items such as T-shirts, uniforms, hats, and socks.
Stable Finish
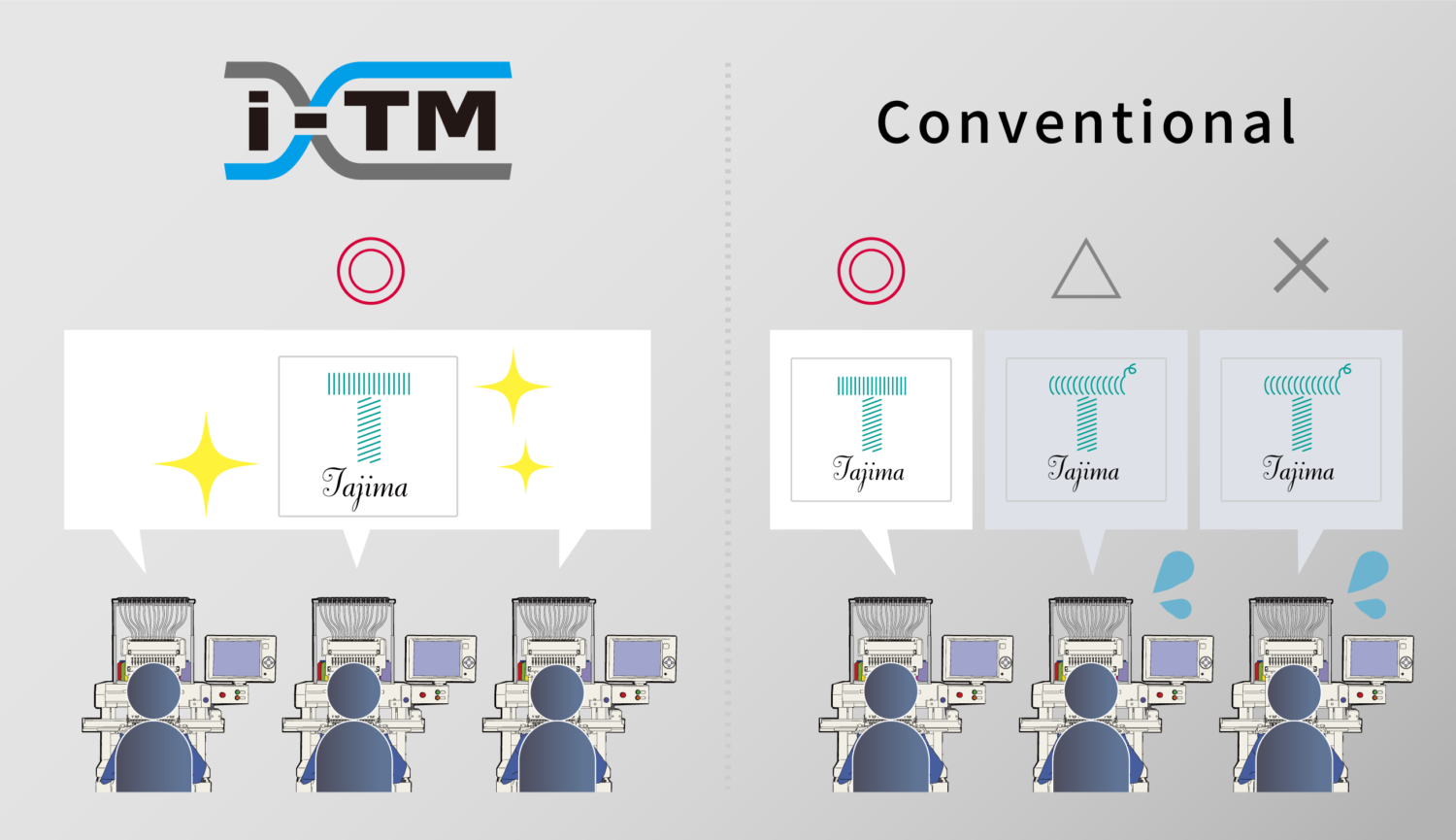
Always the same finish, even if the operator changes
Operators no longer need to make adjustments according to various conditions such as design, material, temperature, and humidity. With i-TM and DCP, stable production is always possible, regardless of operator skill. In addition, The DCP reduces fabric fluttering, resulting in fewer press marks and thread trimming errors, and thus fewer defective pieces. Manual adjustment for delicate fabrics such as velvet and enameled material reduces the risk of fabric press marks.
Productivity Improvements
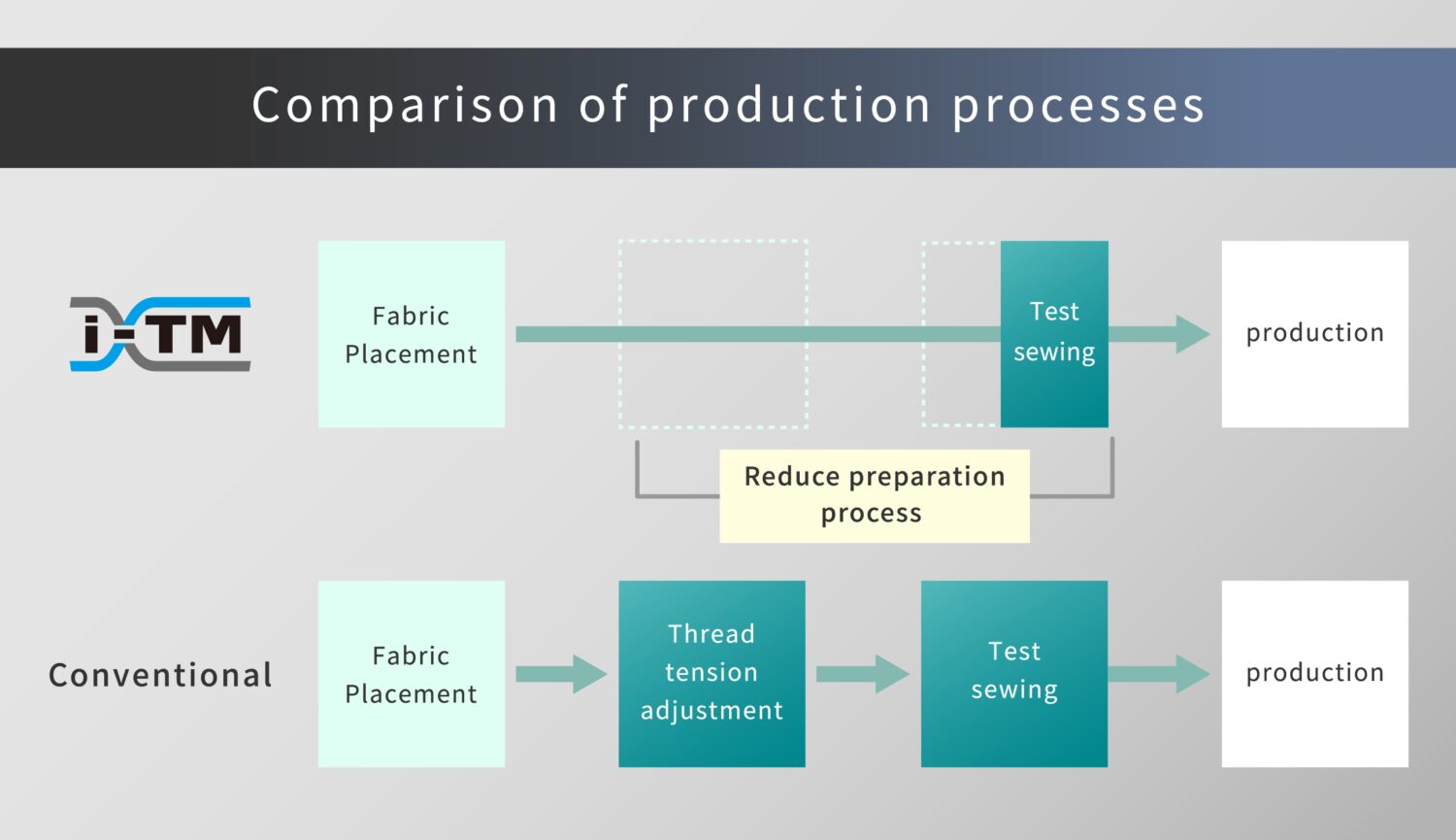
Increasing production per operator
The time required for trial sewing and adjustment can be reduced, and the speed can be increased with less worry of thread breakage, resulting in an estimated 30% reduction in processing time (compared to conventional machines). Less adjustment work allows multiple embroidery machines to be controlled at the same time, increasing production per operator.
Effective examples of “i-TM + DCP”
Lace Embroidery
Even on lace embroidery where satin stitches and running stitches are mixed, the amount of thread required for each stitch is automatically calculated and supplied, allowing you to sew with the optimal thread tension. By using voluminous satin stitches and tight running stitches, you can sew neatly without clogging the seams.
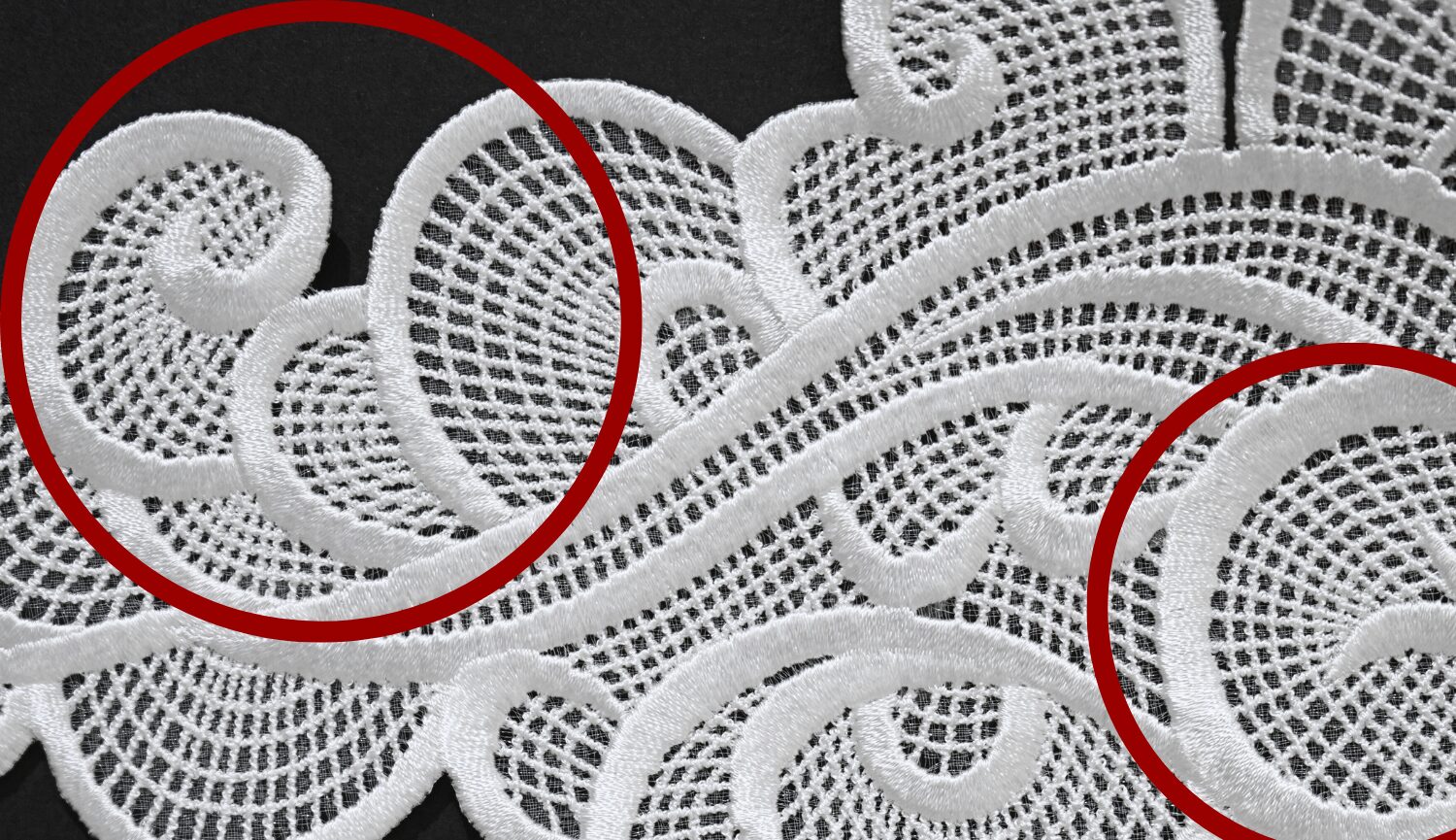
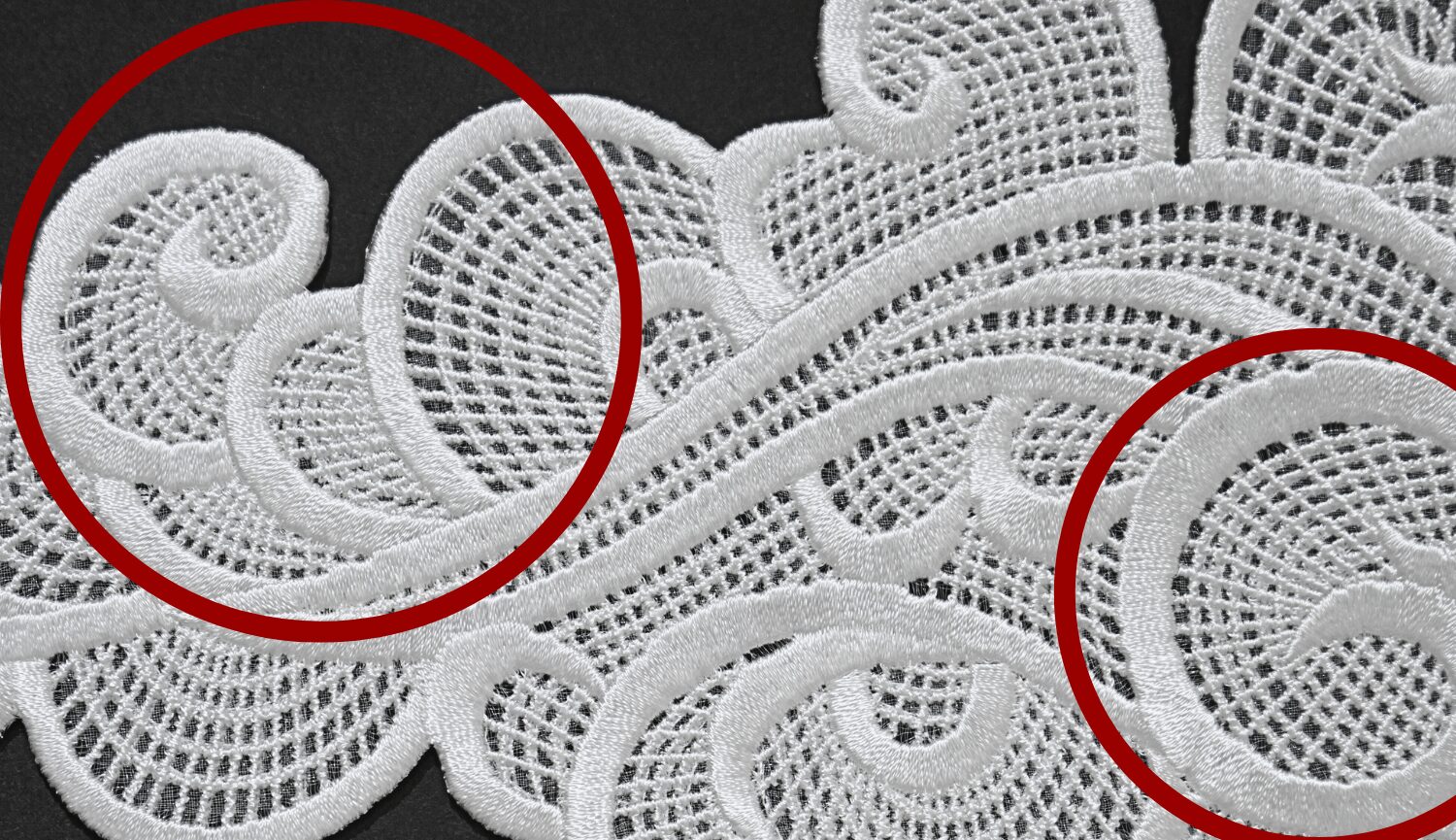
3D Embroidery
The thickness of the urethane foam is measured for each stitch, DCP automatically applies proper pressure based on material thickness and the amount of thread supplied is automatically adjusted, allowing you to sew voluminous 3D embroidery without excessively crushing the urethane foam.
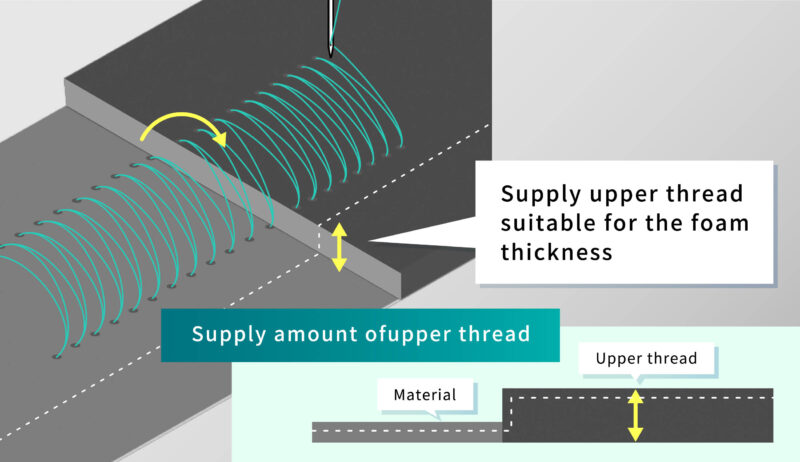
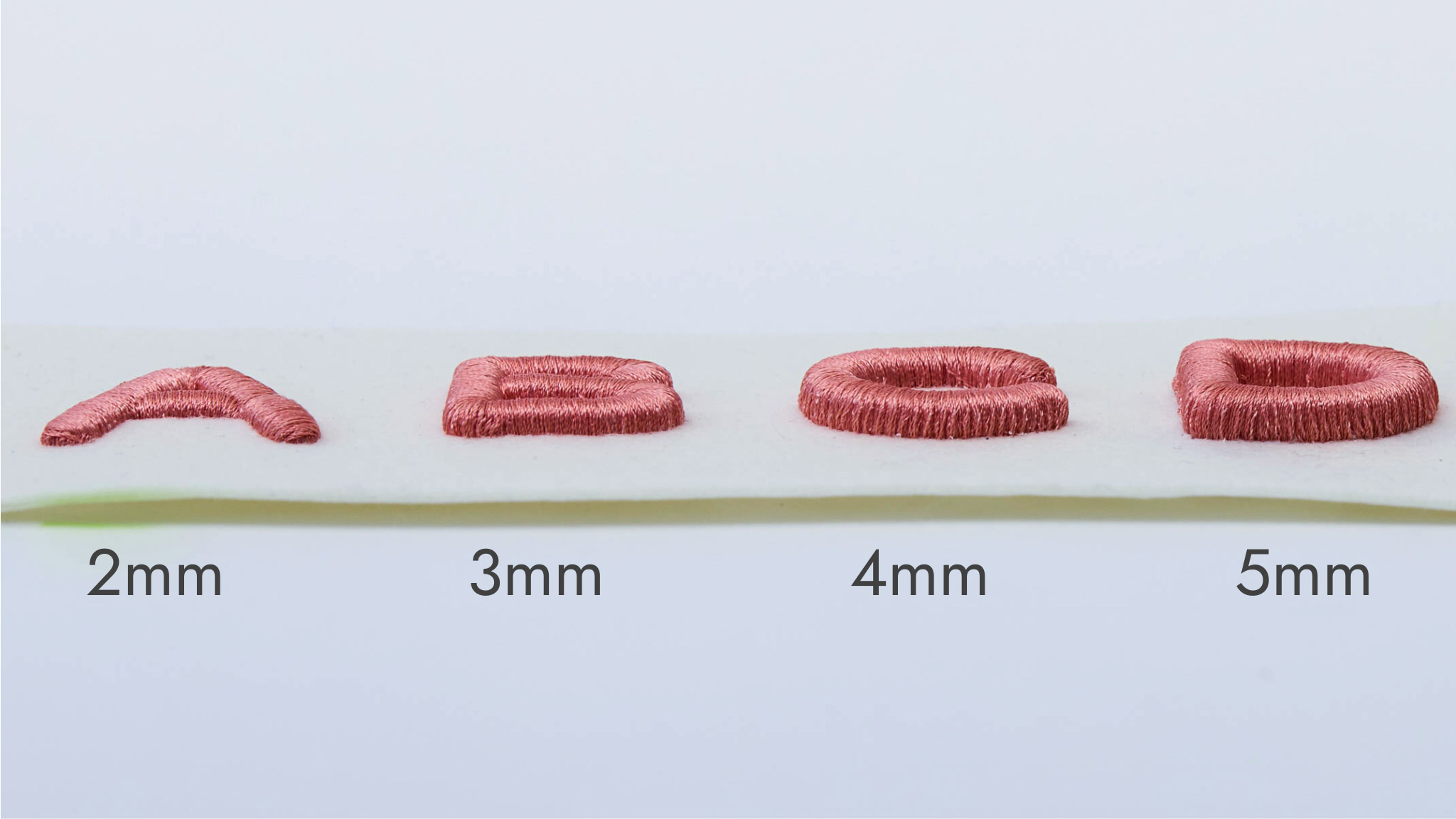
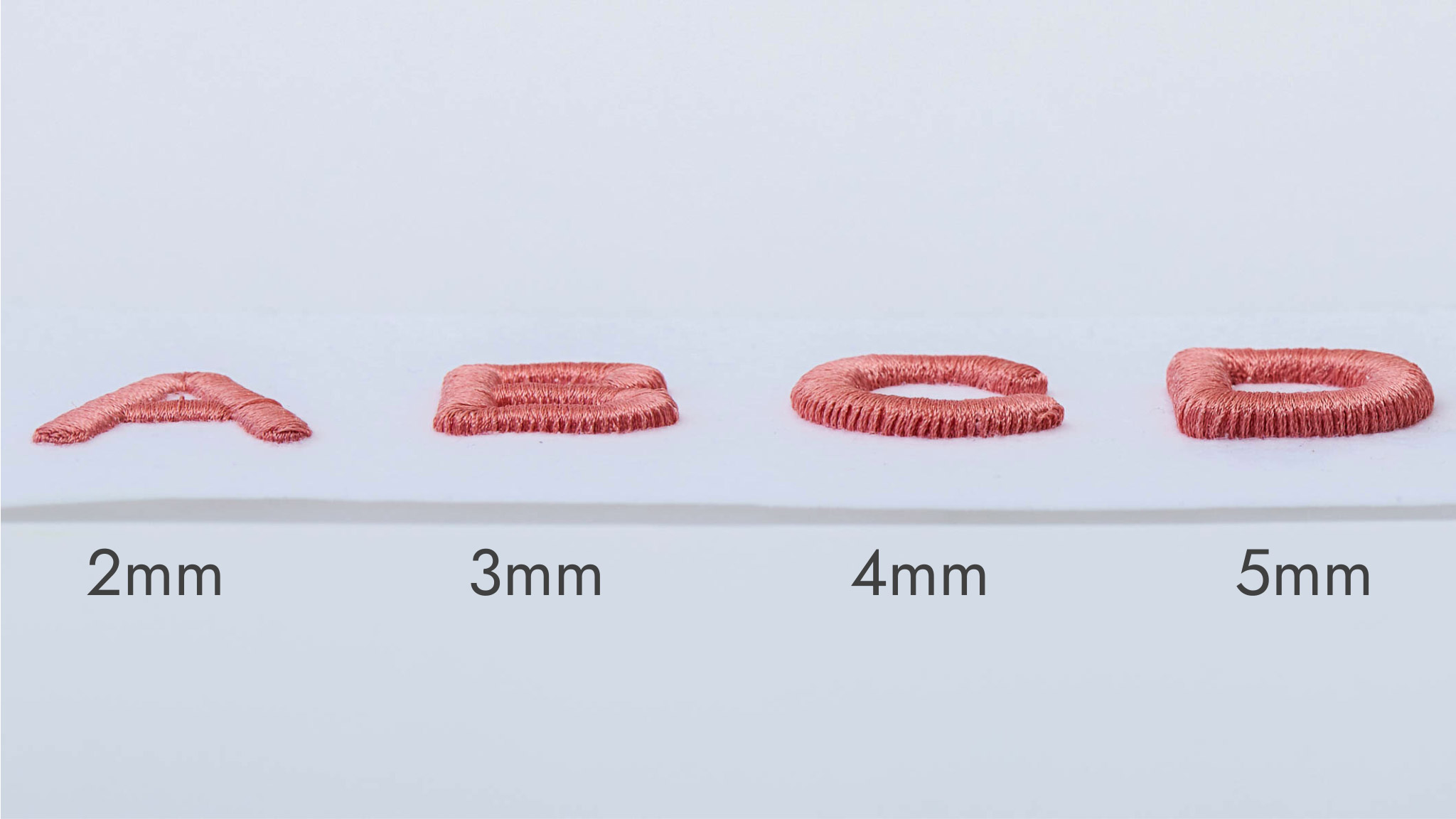
The back side of thick leather products
Even for thick leather materials, DCP applies proper pressure to hold the fabric securely. In addition, i-TM maintains proper upper thread tension so that the thread is pulled up firmly and the back side of the embroidery is finished beautifully.
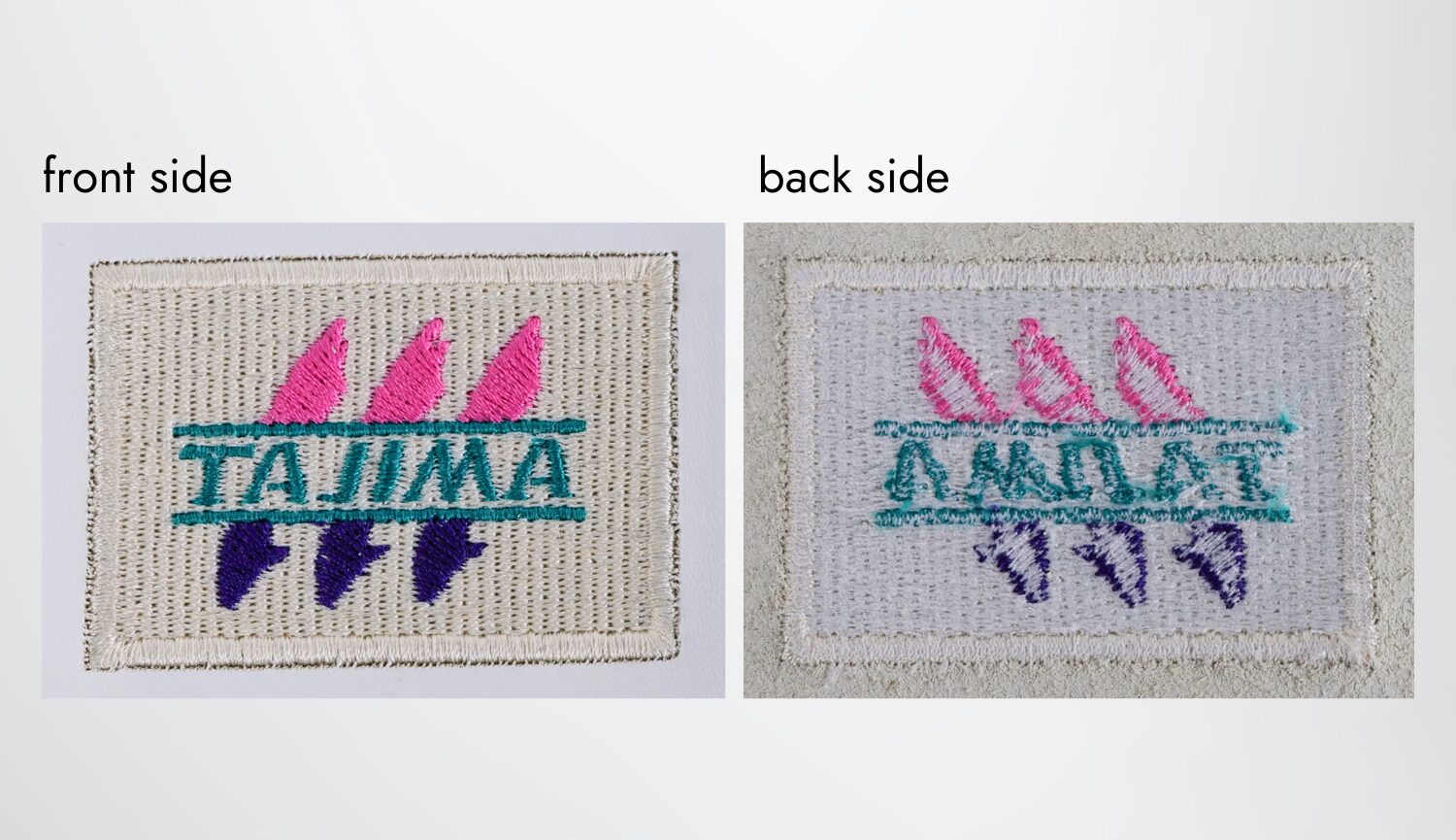
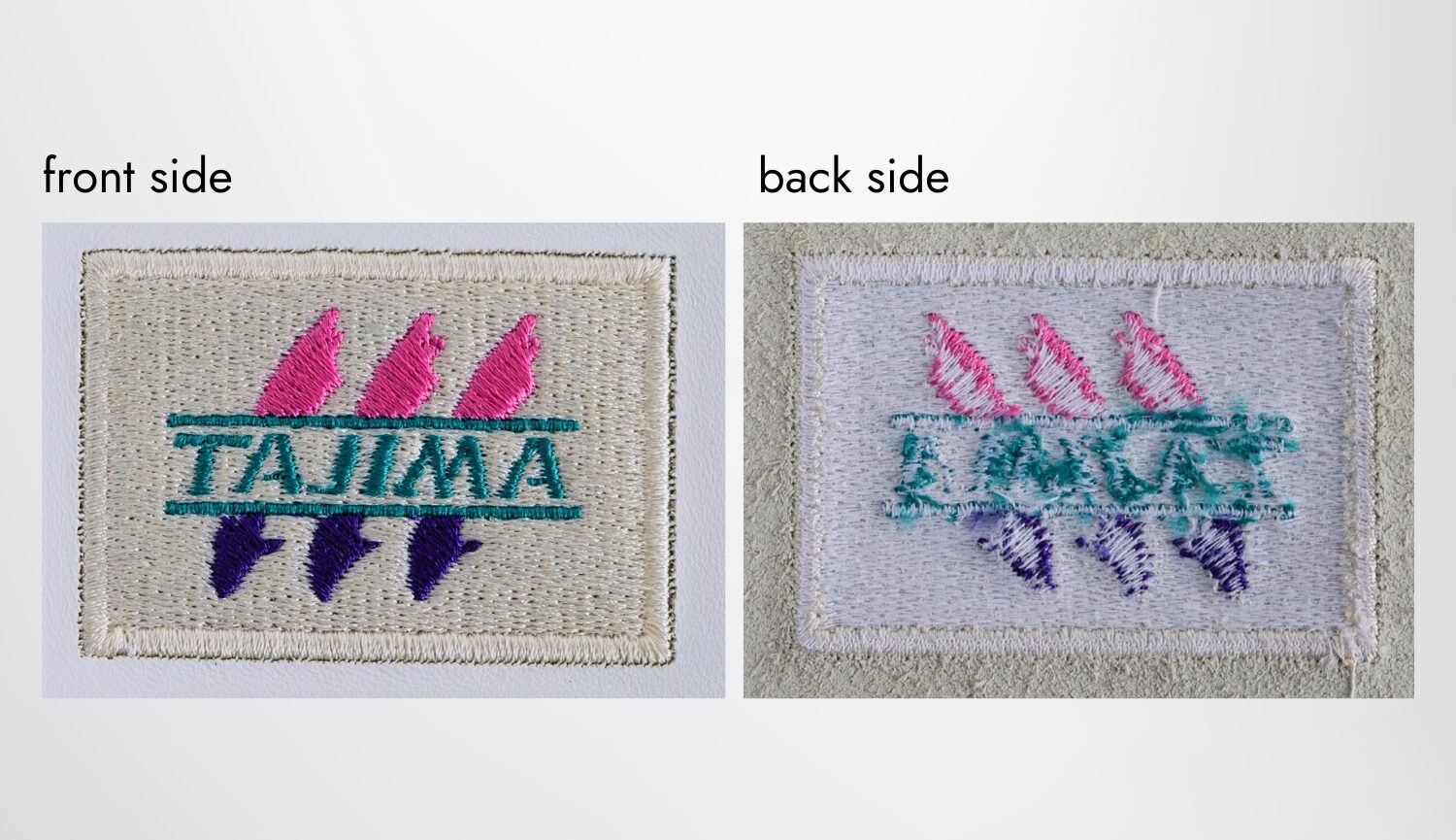
Customer Feedback
Many of our customers appreciate Tajima’s AI technology, i-TM.
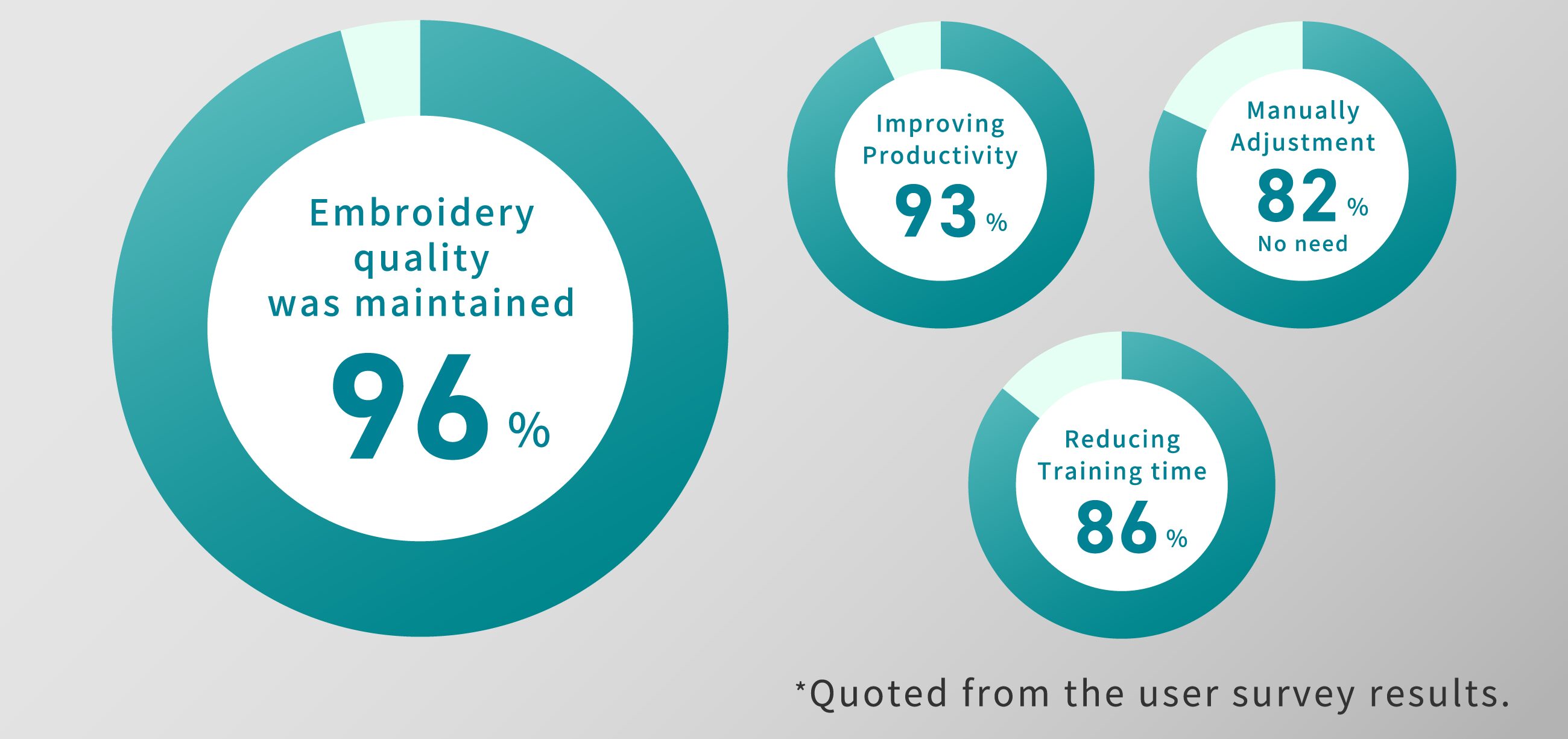
Products Featuring “i-TM + DCP”
-
Embroidery machine|Single-head Cylinder Type
TMEZ-SC
Single-head Cylinder Type Flagship Model is equipped with Tajima's latest technologies
- Flagship
-
-
Embroidery machine|Multi-head Cylinder Type
TMEZ-KC
Multi-head Cylinder Type Flagship Model is equipped with Tajima's latest technologies
- Flagship
-
-
Embroidery machine|Multi-head Flat Type
TMCR-VF+i-TM
Multi-head Flat Type Flagship Model is equipped with Tajima's latest technologies
- Flagship
-
TAJIMAG
Recommended content
-
Dialogue・Special feature
Tabio Co., Ltd. | Creating new value through embroidery. Producing one-of-a-kind socks, unique in all the world.
-
Customer’s voice
Tabio Nara Co., Ltd. | Introduction of the DG.NET embroidery solution creates new ways to enjoy embroidery!
-
Customer’s voice
Kutsushitaya Kichijoji store|Embroidery Services Fulfilling Customers’ Wishes Custom embroidery socks in just 30 minutes!