CFRP— An Essential Material in Achieving Carbon Neutrality
What is carbon fiber reinforced plastic, or CFRP?
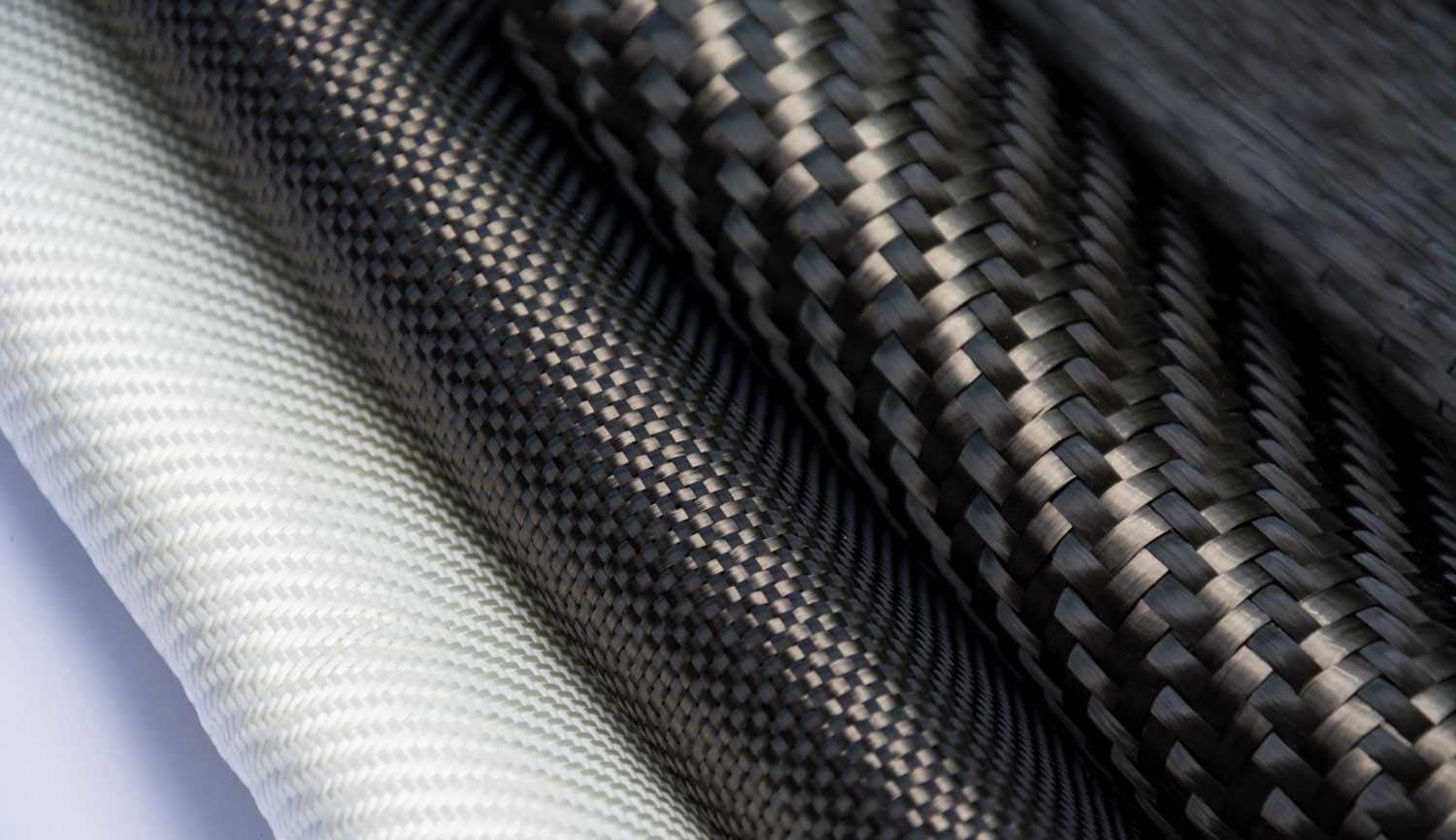
CFRP(Carbon Fiber Reinforced Plastics)
CFRP is a composite material made by reinforcing plastic (synthetic resin) with carbon fiber. Lightweight, very strong, and highly rigid (resistant to bending or sagging), it is used in a wide range of industrial fields, from sporting goods to aircraft components and automotive parts.
[Advantages of Reinforced Fibers]
Light and durable
Highly wear-, heat-, and acid-resistant and also features excellent electrical conductivity
Examples of Products Utilizing CFRP
Manufacturing CFRP parts using conventional carbon cloth
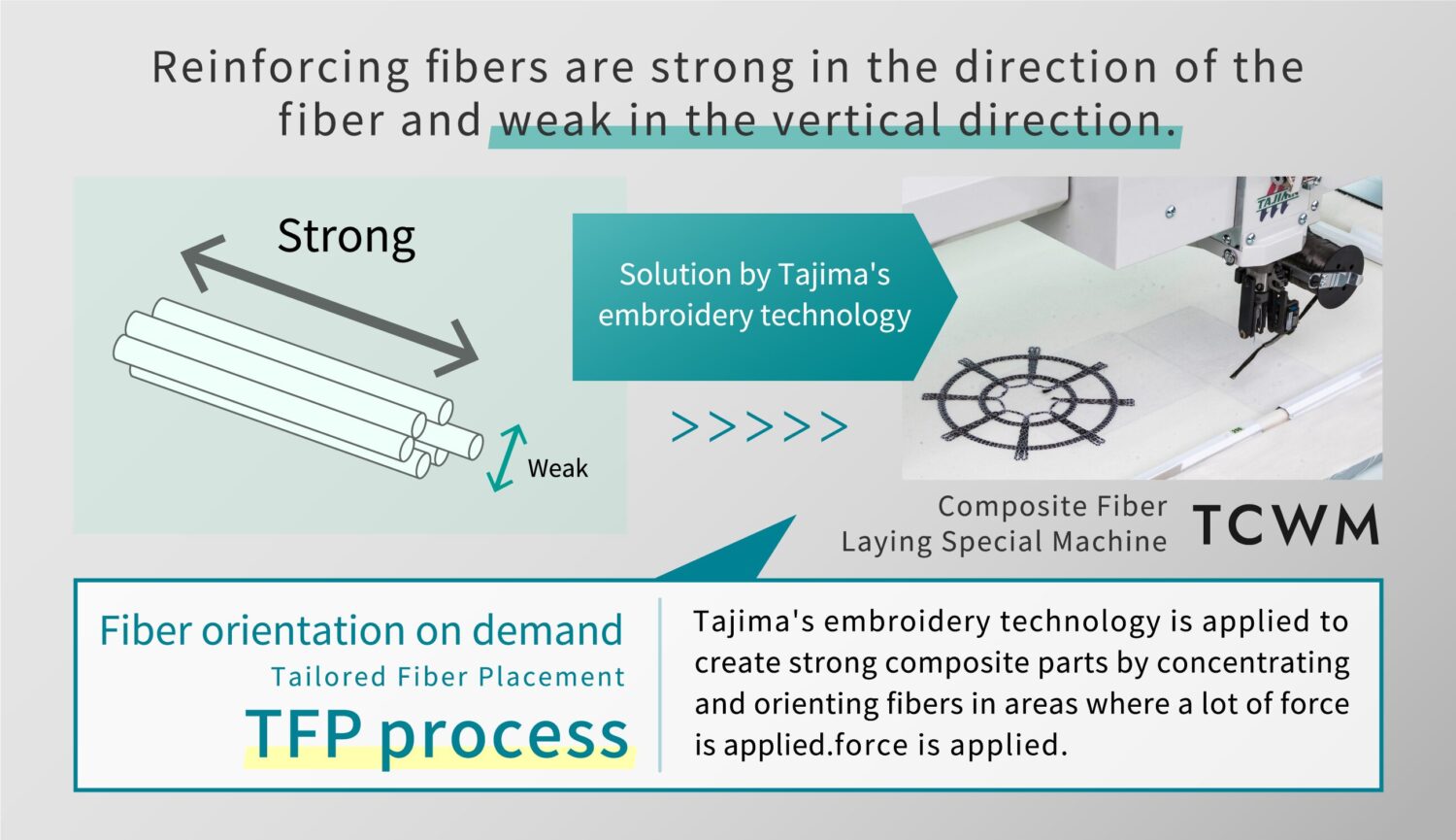
Conventional manufacturing process have numerous disadvantages
CFRP is generally formed through lamination using carbon cloth. However, CFRP is a highly anisotropic material that only exhibits strength in the direction of the fiber’s orientation, thus it is difficult to make full use of the material’s properties when manufacturing CFRP with carbon cloth. This manufacturing process also has a low yield rate, since the laminated carbon cloth is cut into arbitrary shapes.
The “TFP process”
Orientation Design That Maximizes the Potential of CFRP Materials
What is the “TFP process?”
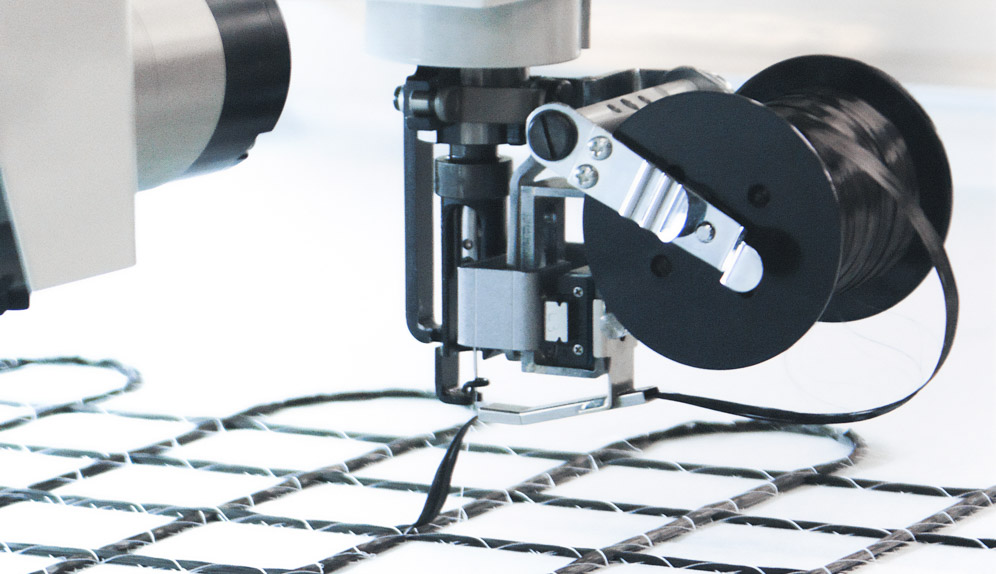
The TFP (Tailored Fiber Placement) process is a process in which reinforcing fibers are sewn onto a base material to form a preform (intermediate base material) with the required properties. Reinforcing fibers such as carbon fibers that exhibit pronounced anisotropy, which provides strength only in the fiber’s orientation, can be arranged continuously and freely, making it possible to design a composite material structure that provides the necessary strength in the required direction, making it possible to create products and components that are both lightweight and highly rigid. Additionally, the fact that these fibers can be oriented with minimal cutting means this process also has a high material yield rate.
Differences with Conventional Construction process
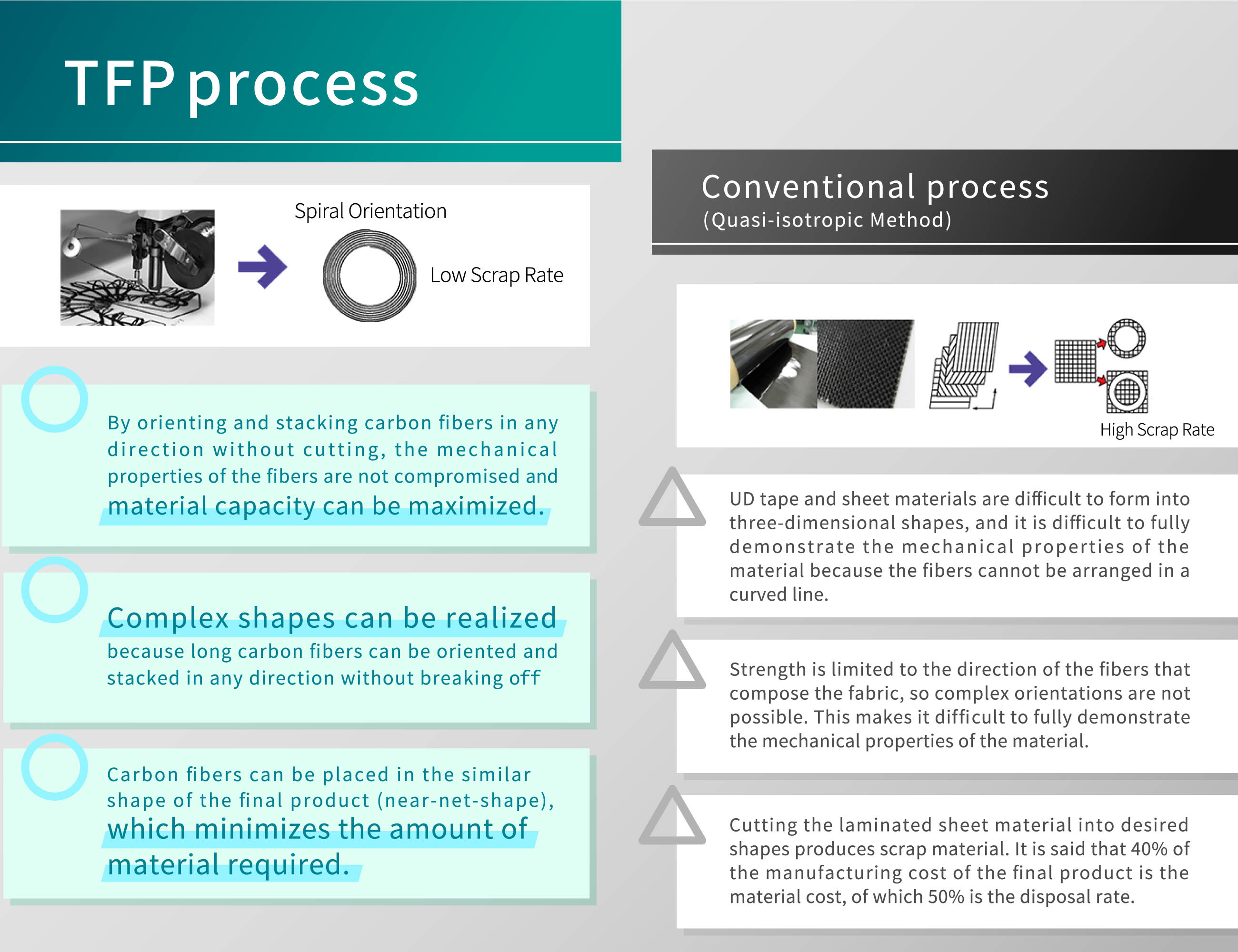
Features of the TFP process
Enables previously impossible orientations for shapes
While simply laminating with conventional unidirectional tape and textile materials is sufficient when stresses are oriented at 0° or 90°, these materials are extremely difficult to use on hollow, spiral, radial, and other more complex shapes, creating major challenges both in terms of manufacturing and strength. The TFP process solves these problems. The fibers can be sewn into various shapes, which allows the creation of complex forms while maintaining strength.
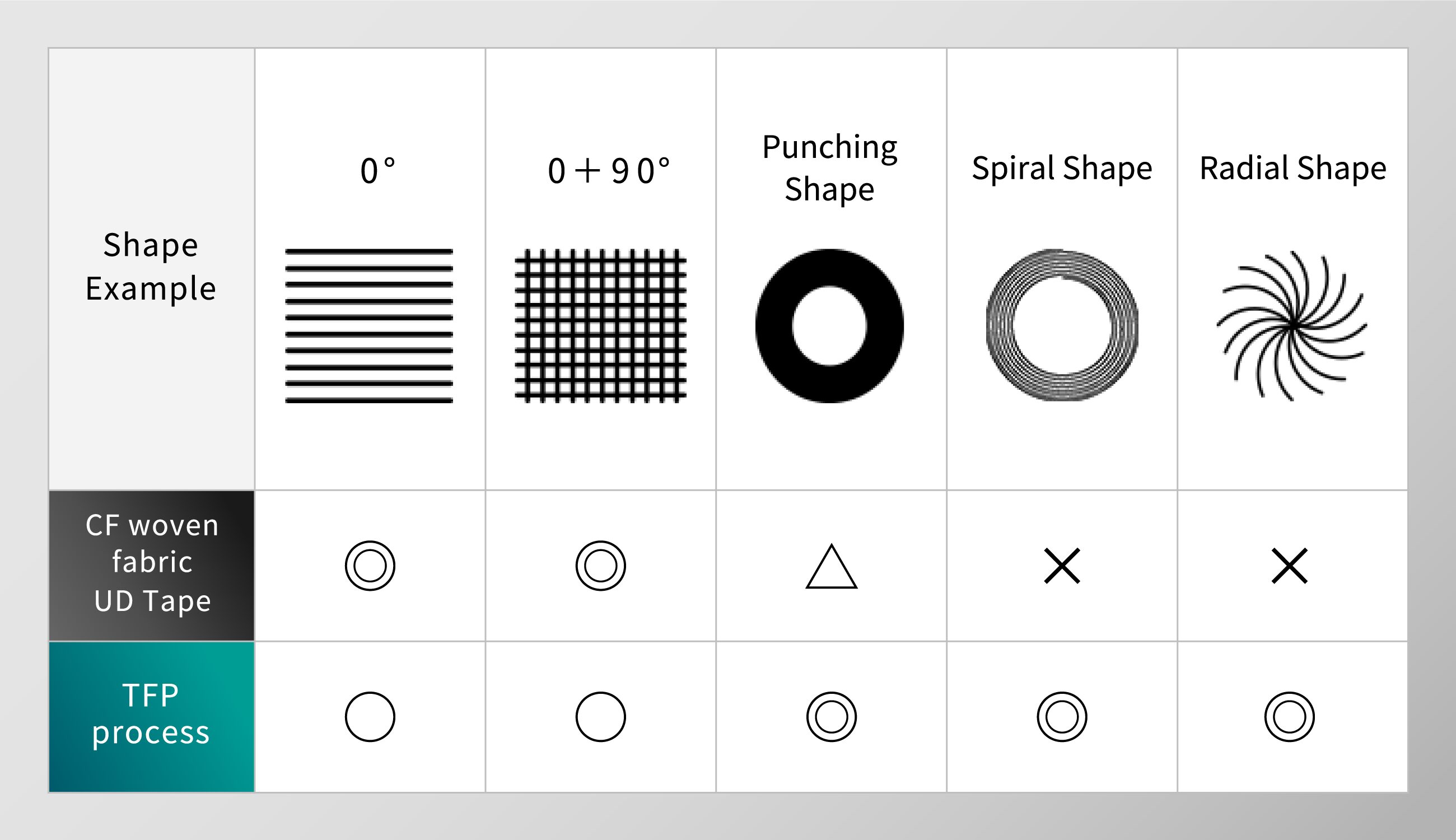
CFRP Enables Orientations Providing Superior Weight Savings, Strength, and Durability
When replacing metal parts with CFRP (carbon fiber reinforced plastic), using the TFP process, which allows fibers to be freely arranged, more effectively orients the long fibers to increase rigidity in the desired direction while reducing weight as well. This enables designs that provide superior strength and durability, even in complex structures in which this was previously impossible.
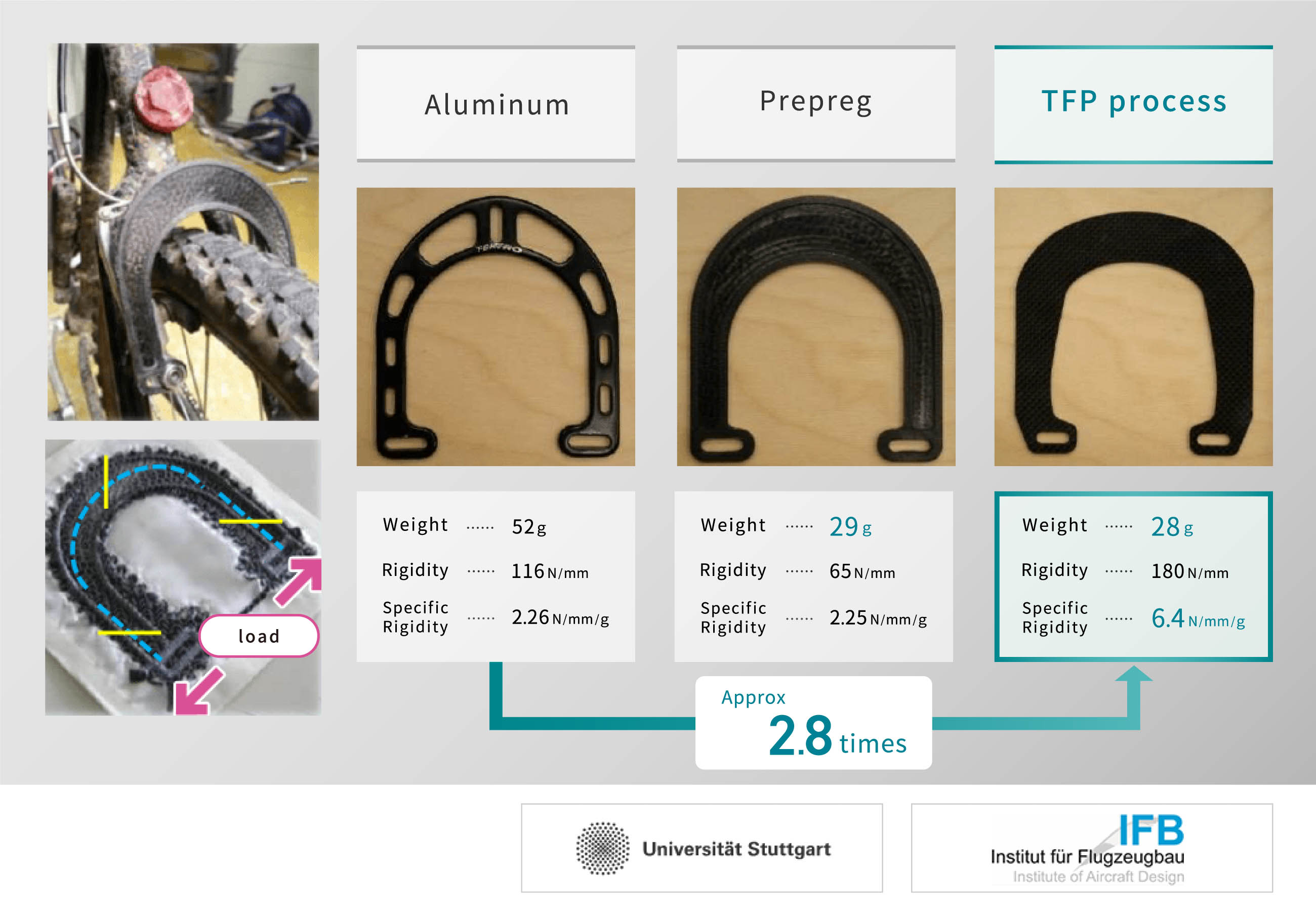
Higher Yield Rate and More Environmentally Friendly Than with Conventional process
With conventional process, laminated sheet materials are cut into arbitrary shapes, resulting in ends and scrap that must be discarded. Material costs account for 40% of the manufacturing cost, and 50% of that is said to be waste. Using the TFP process allows fibers to be oriented in a shape approximating that of the final product (near net shaping) without cutting, making it possible to achieve orientation with a better material yield rate.
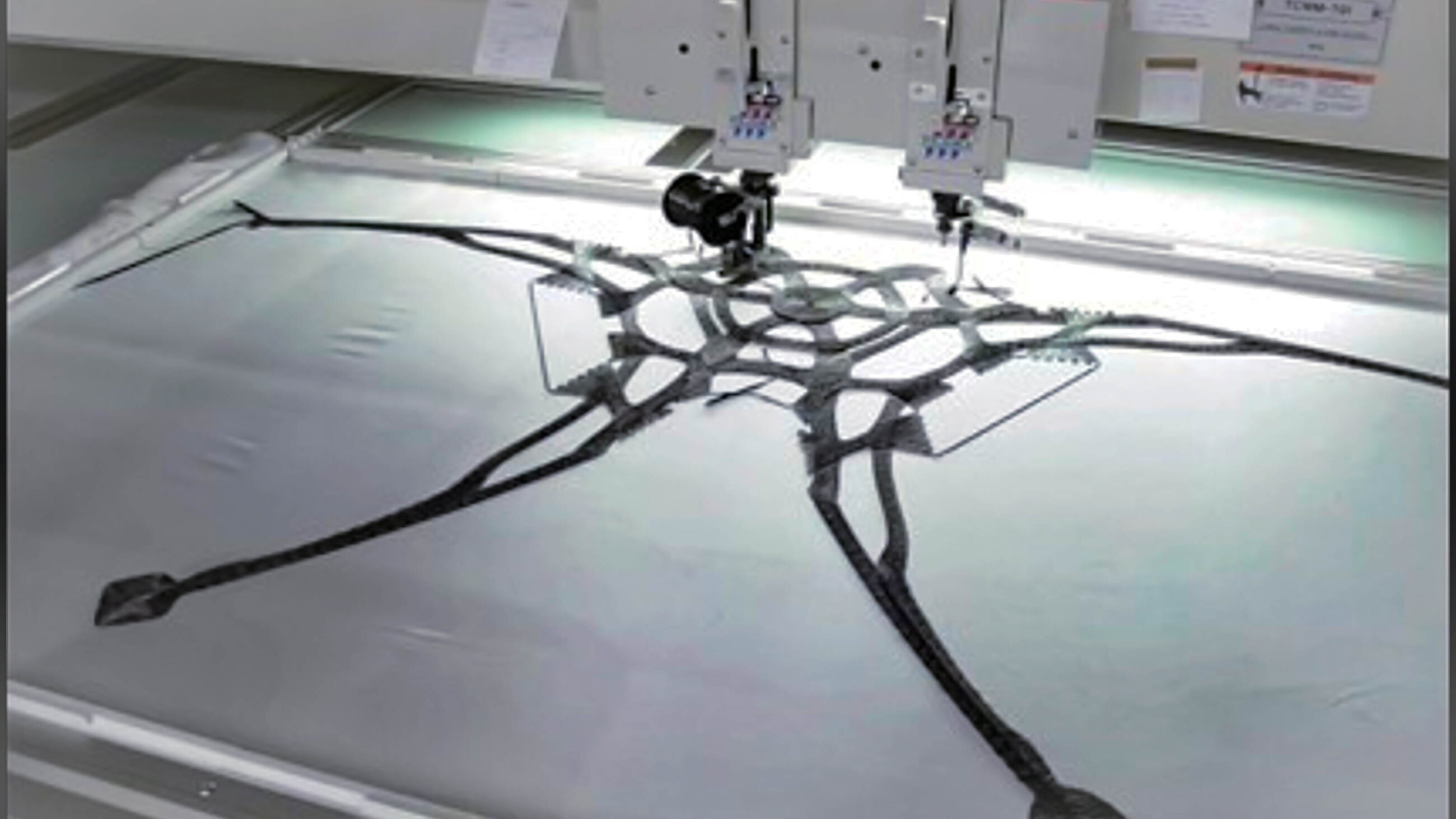
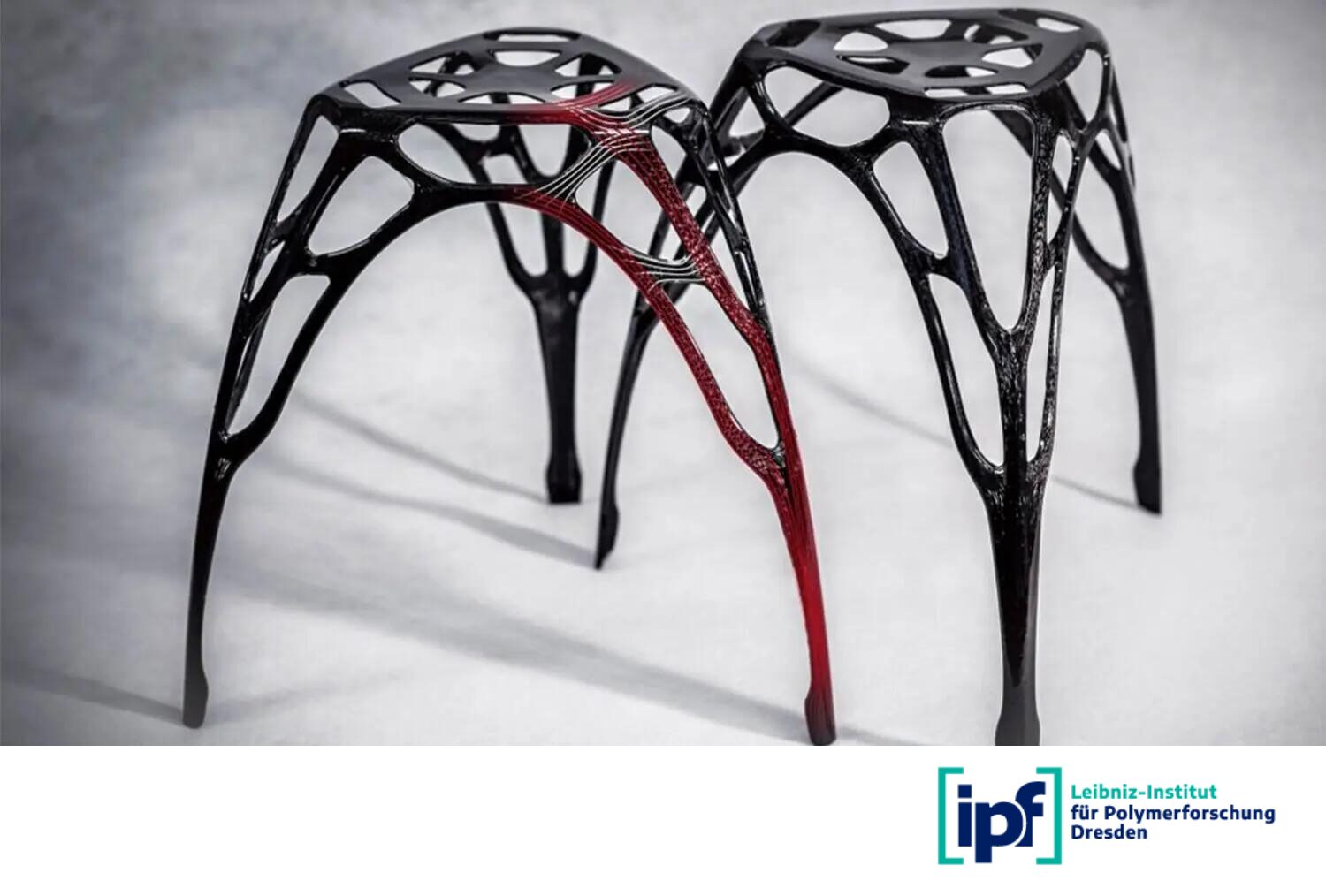
Orientation Design and Preform Production Sequence Using the TFP process
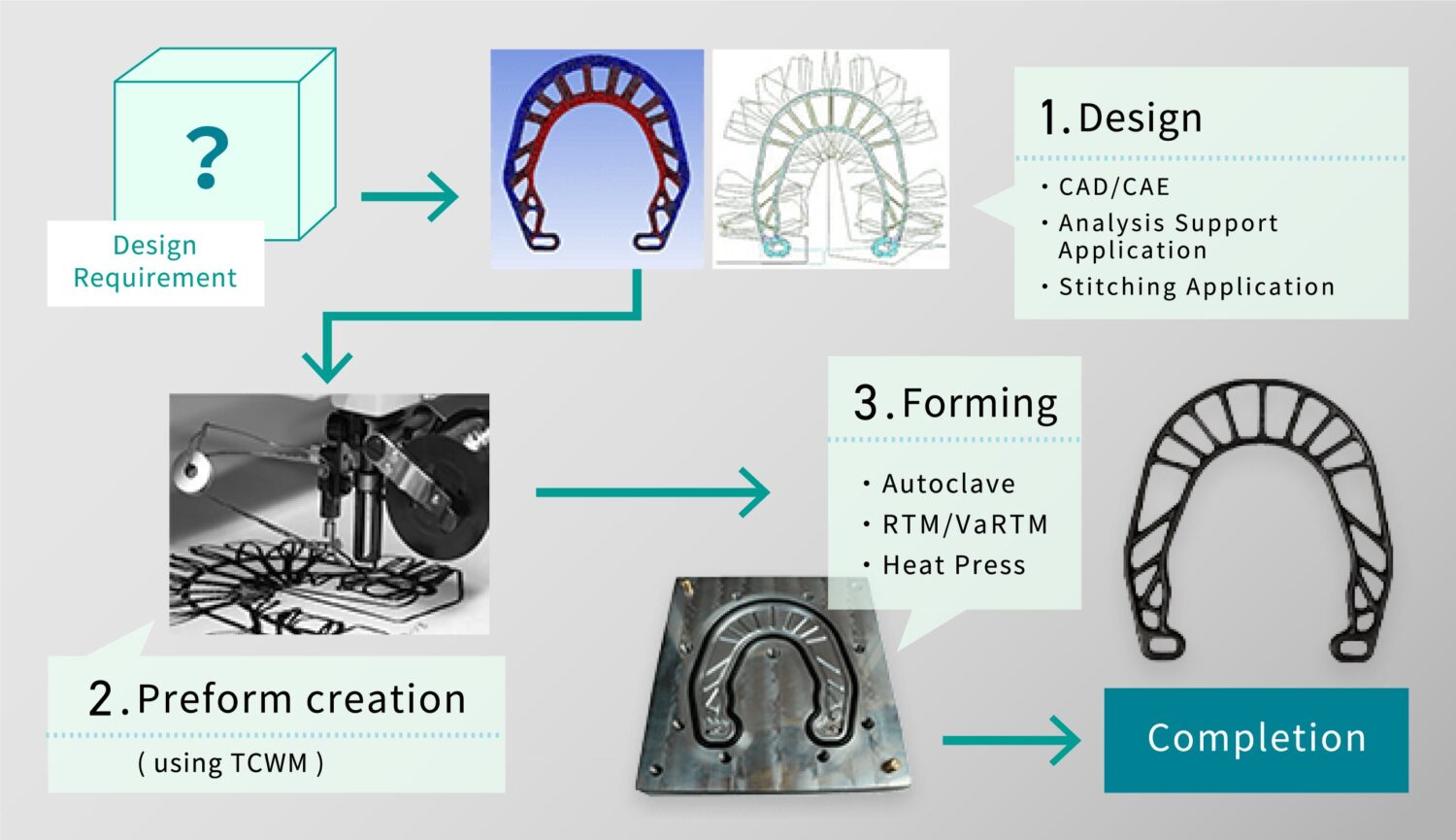
We not only provide consultations on using to the TFP process in prototyping, fiber orientation design, and preform (intermediate base material) production, we also welcome inquiries from those who are encountering limits in FRP’s material capabilities and those who want to more fully leverage FRP’s characteristics. Please feel free to contact us.
Recommended Products
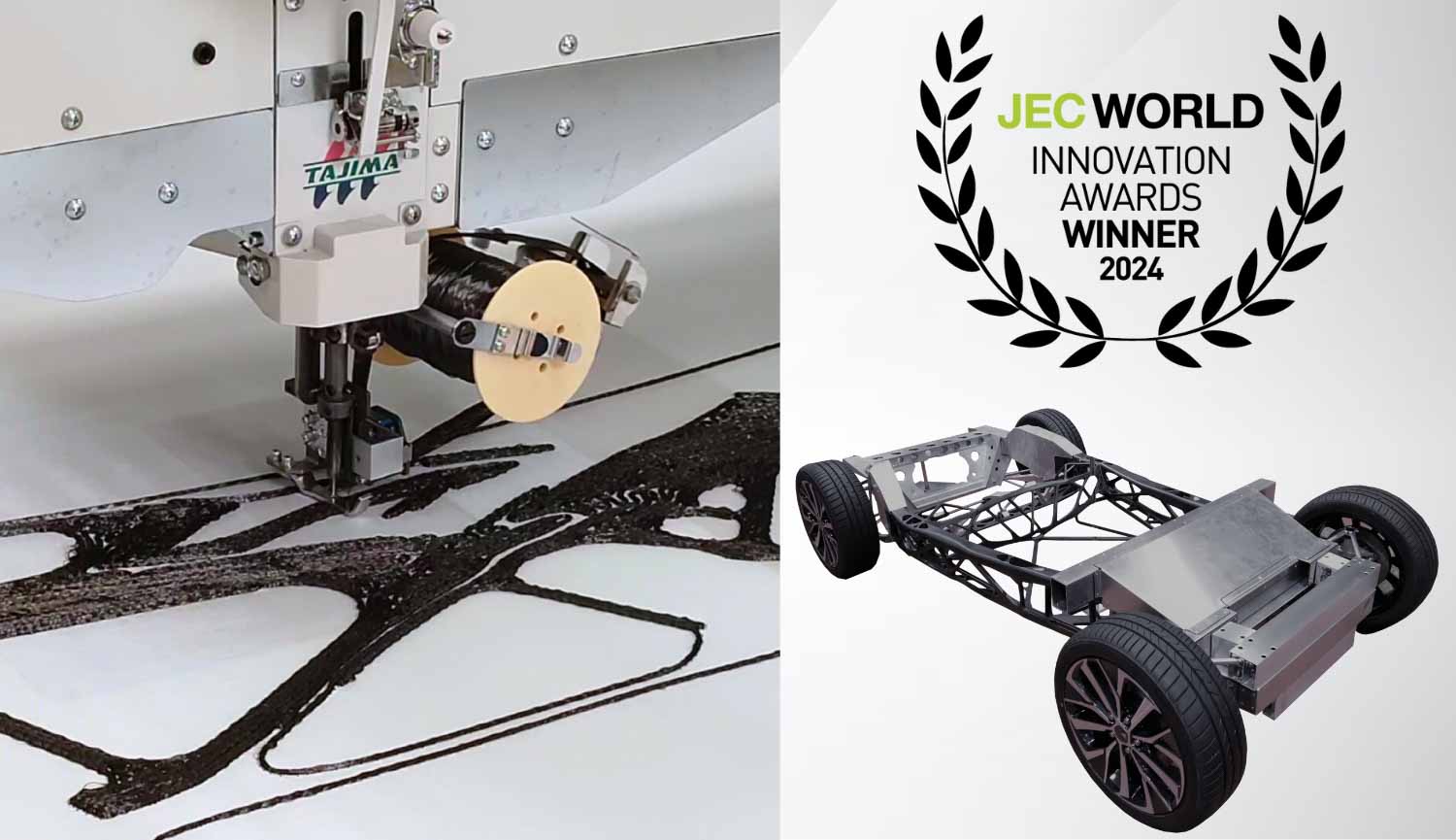
Won the “JEC COMPOSITES INNOVATION AWARDS”
The production of a” Monolithic CFRP-Aluminum Monocoque,” which was undertaken by four companies (*) including TISM Co., Ltd. , has won the “JEC COMPOSITES INNOVATION AWARDS AUTOMOTIVE & ROAD TRANSPORTATION-PARTS Category Award.
*Toyota Motor Corporation (Japan), Toyota Central R&D Labs., Inc (Japan), Toyota Customizing & Development Co., Ltd. (Japan), TISM Co., Ltd. (Japan)