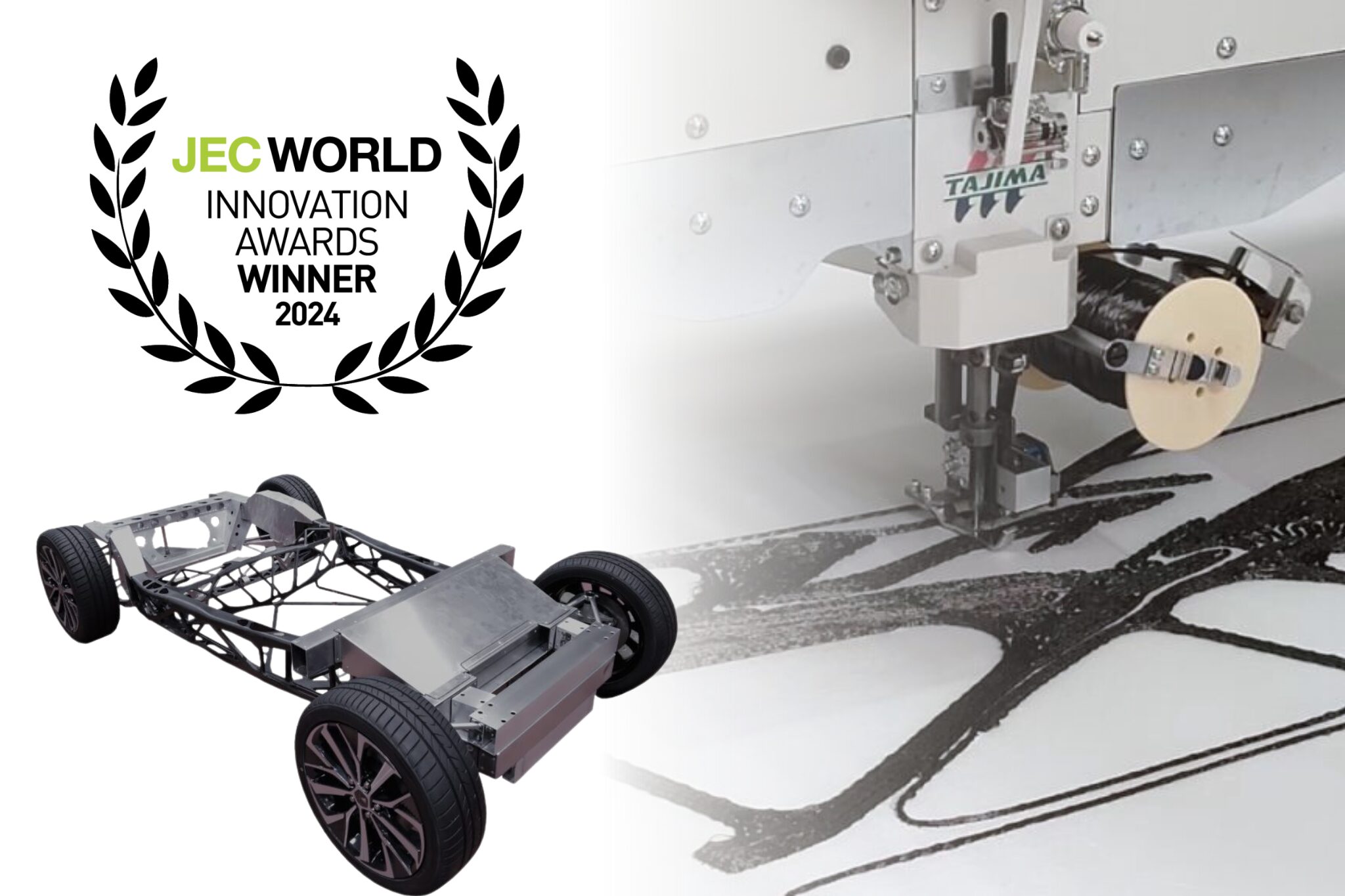
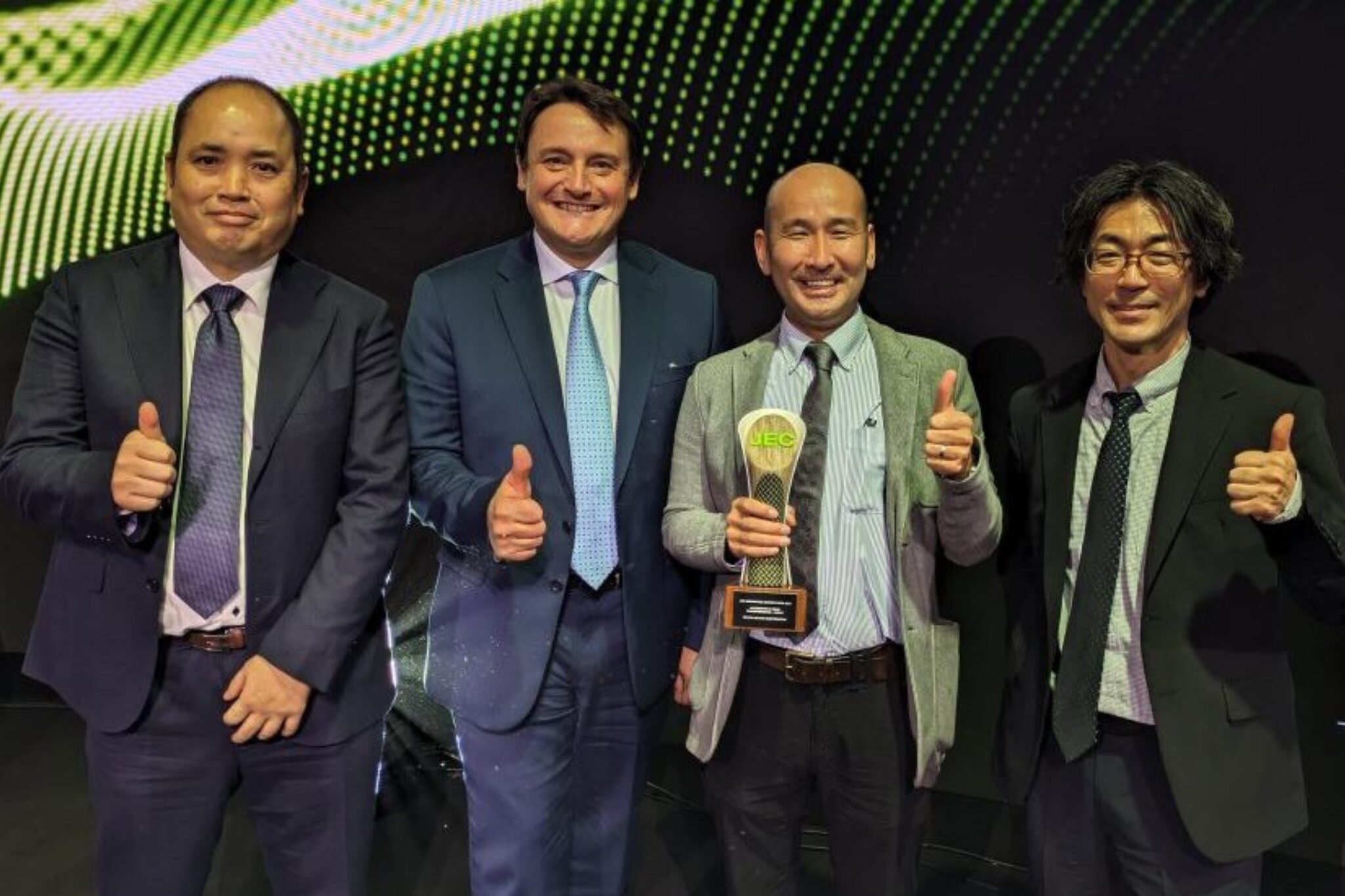
In February 2024, the Tajima Group’s development arm TISM won the JEC Composites Innovation Awards Automotive & Road Transportation–Parts’ category for their monolithic CFRP-aluminum monocoque.
Conferred by France’s JEC Group, this international award recognizes cutting-edge, innovative projects that best demonstrate the potential of composite materials.
The project was honored for its successful demonstration of a full-scale vehicle monocoque made from a composite of CFRP (carbon fiber reinforced plastic) and aluminum, designed to advance carbon neutrality.
How was Tajima’s embroidery technology utilized in this project involving a collaboration between four companies*?
We interviewed Ohashi, the Advanced Technology Development Department of TISM Co., Ltd.
*Toyota Motor Corporation, Toyota Central R&D Labs Inc., Toyota Customizing & Development Co., Ltd., TISM Co., Ltd.
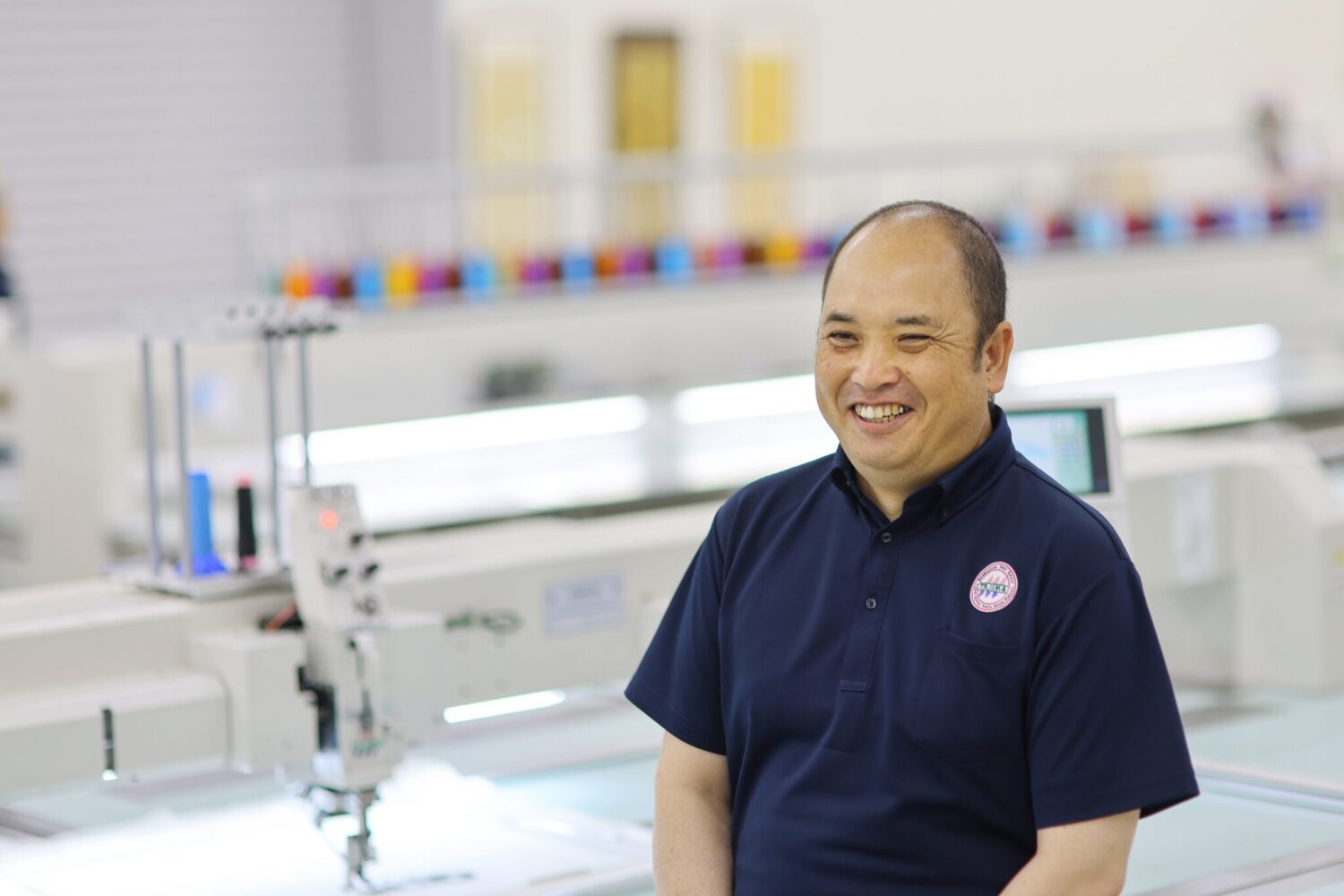
Honored with an international award for composite material technology.
TISM Co., Ltd
Advanced Technology Development Department
Isao Ohashi
TFP Process Shows Tremendous Potential
In this project, four companies, including TISM, collaborated in a demonstration experiment to produce a full-scale vehicle monocoque with a structure integrating CFRP and aluminum. The CFRP component used “TFP (Tailored Fiber Placement)” technology, where reinforcing fibers are sewn onto a base material to form a preform (intermediate base material).
The Tajima Group was among the first to recognize the potential of the TFP process while exploring new applications for embroidery technology and has since been dedicated to advancing this technology.
One individual who has been consistently involved in the development of the TFP process since around 2015 is Ohashi of the Advanced Technology Development Department.
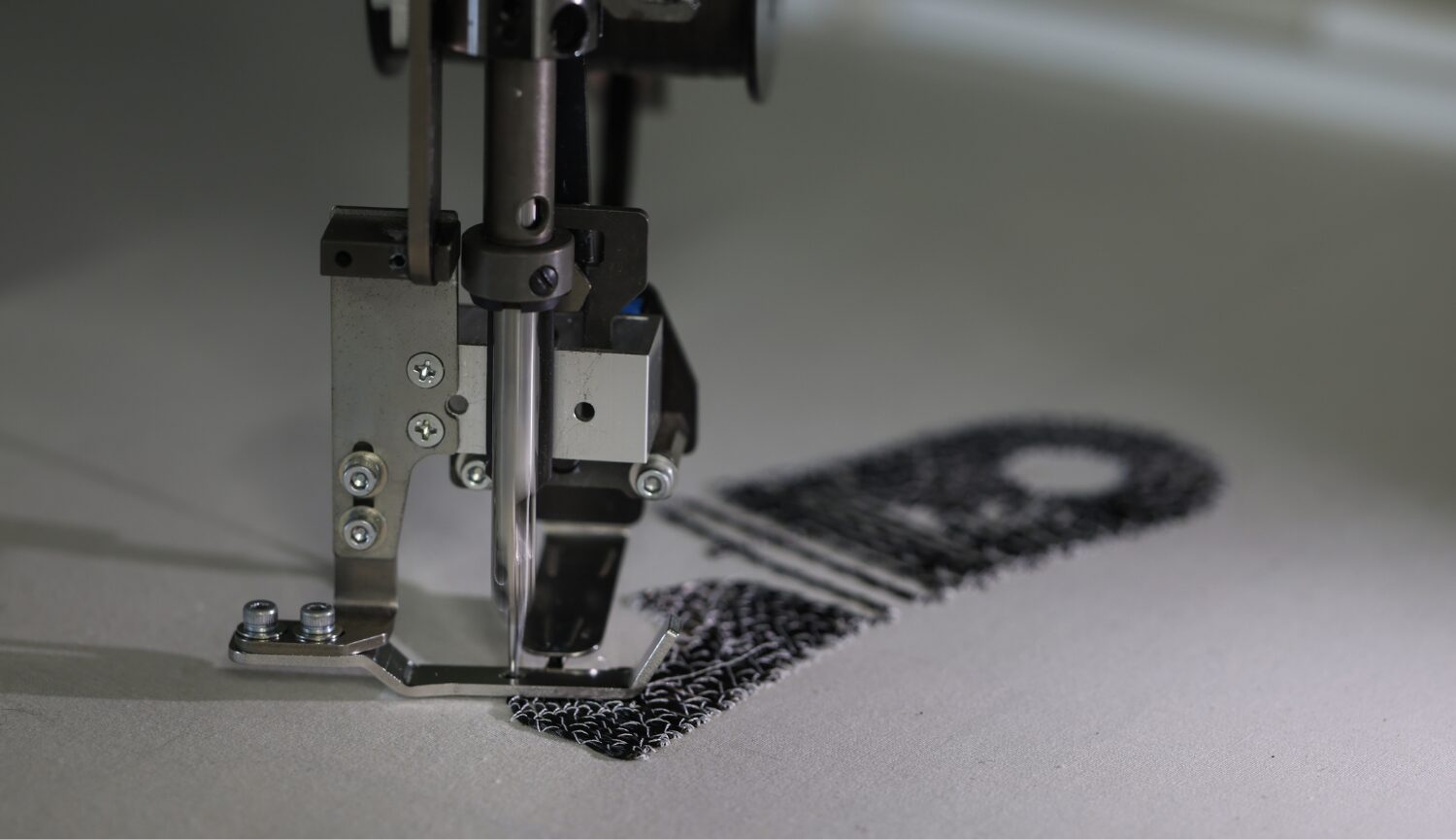
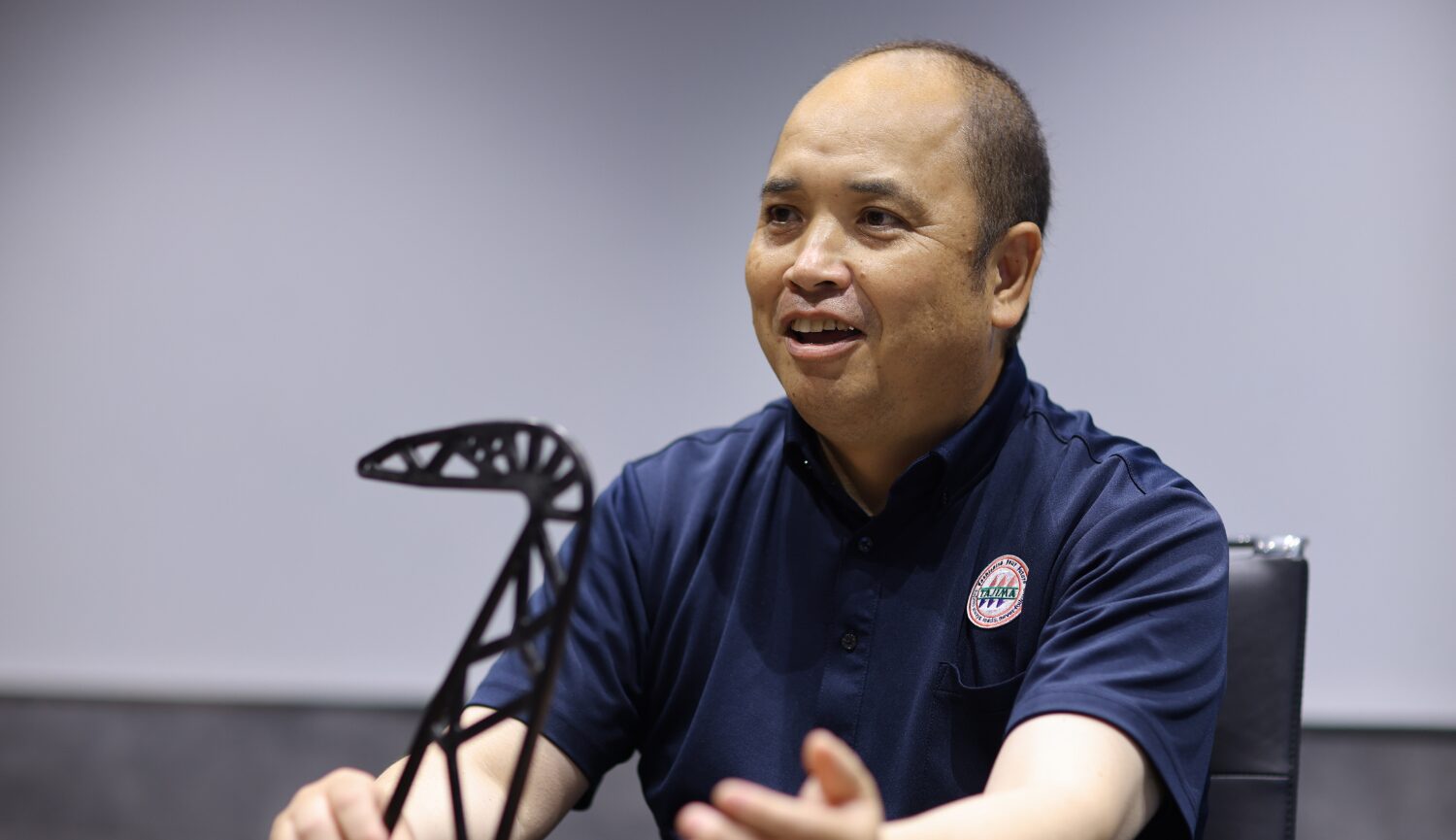
“When I first joined the company, I worked in the Manufacturing Department, where I was responsible for embroidery machine assembly. Later, I was transferred to the R&D Department and began working on the TFP process. The president at the time was very enthusiastic, saying, ‘The TFP process has great potential. We must push forward with it.’ So, he assembled a team and initiated development to bring it to fruition.” Ohashi recalls.
The general process for manufacturing CFRP parts involved molding them using carbon cloth, which is a fabric made of woven fibers. However, CFRP exhibits high strength and rigidity only in the longitudinal direction of the fibers, making carbon cloth unsuitable for molding hollow, radial, or other complex shapes, or for aligning fibers in various directions. Additionally, cutting the laminated sheet material produced large amounts of scrap, leading to low material yield.
The TFP process addresses the limitations of conventional process. It allows reinforcing fibers to be aligned not only in straight lines but also in curves and other directions, enabling the creation of complex shapes while maintaining strength. Moreover, since the fibers are aligned without cutting, material waste is minimized. This process truly maximizes the potential of CFRP.
More about TFP
Making a Full-Scale Vehicle Monocoque
The development of the TFP process, however, was far from smooth. Developing the technology to sew the fibers in their optimal positions was particularly challenging, and the implementation process was a long and difficult journey.
Efforts to achieve the optimal fibers focused on improving the embroidery machine and developing new control systems. All that trial and error finally paid off with the release of the “TCWM” specialized composite fiber sewing machine in 2009.
The key feature of the TCWM is its ability to accurately sew reinforcing fibers using a computer-controlled sewing head. The sewing angle can be freely adjusted from 0° to 360°, allowing the fibers to be precisely oriented to match the shape of the final product.
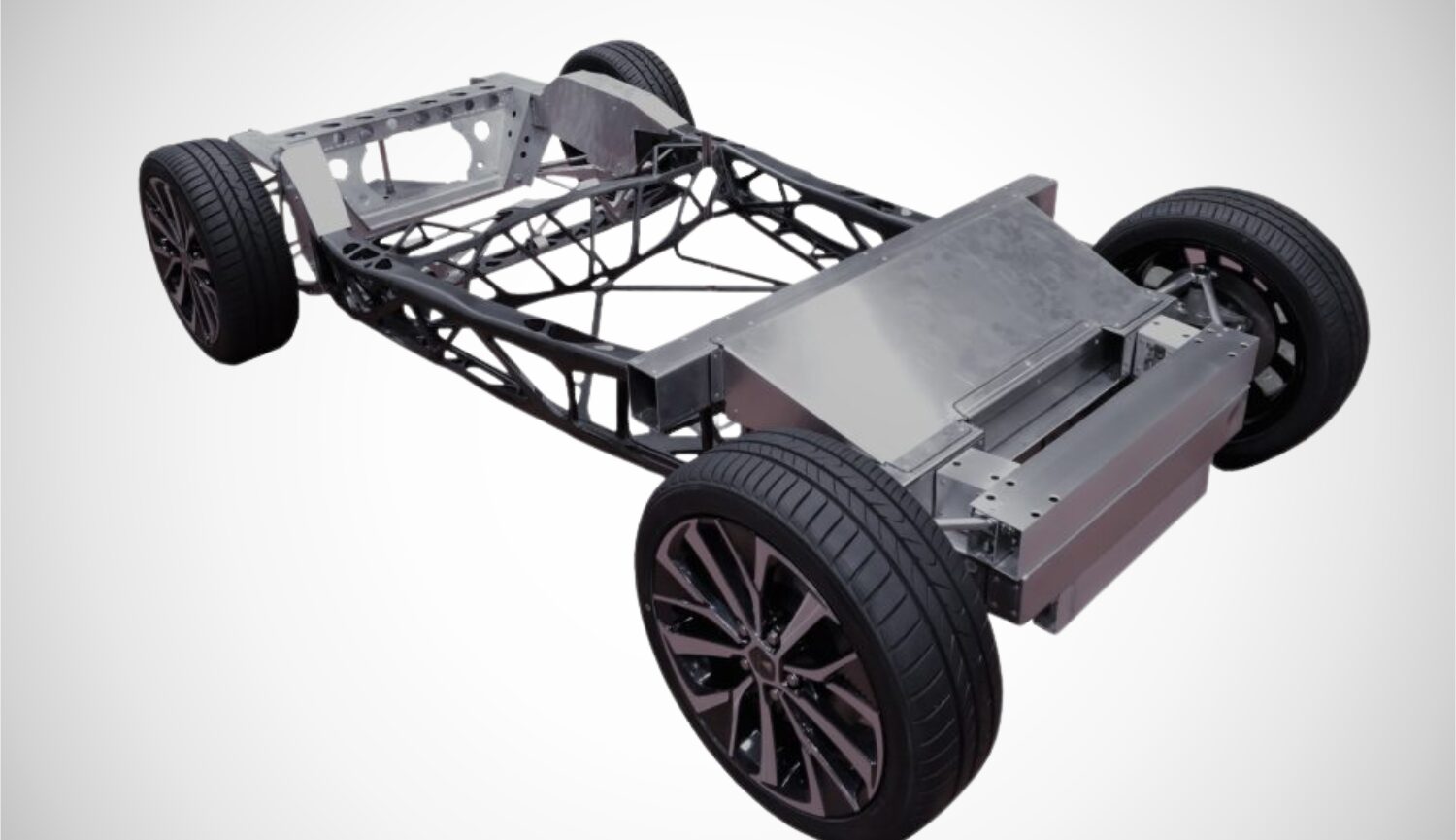
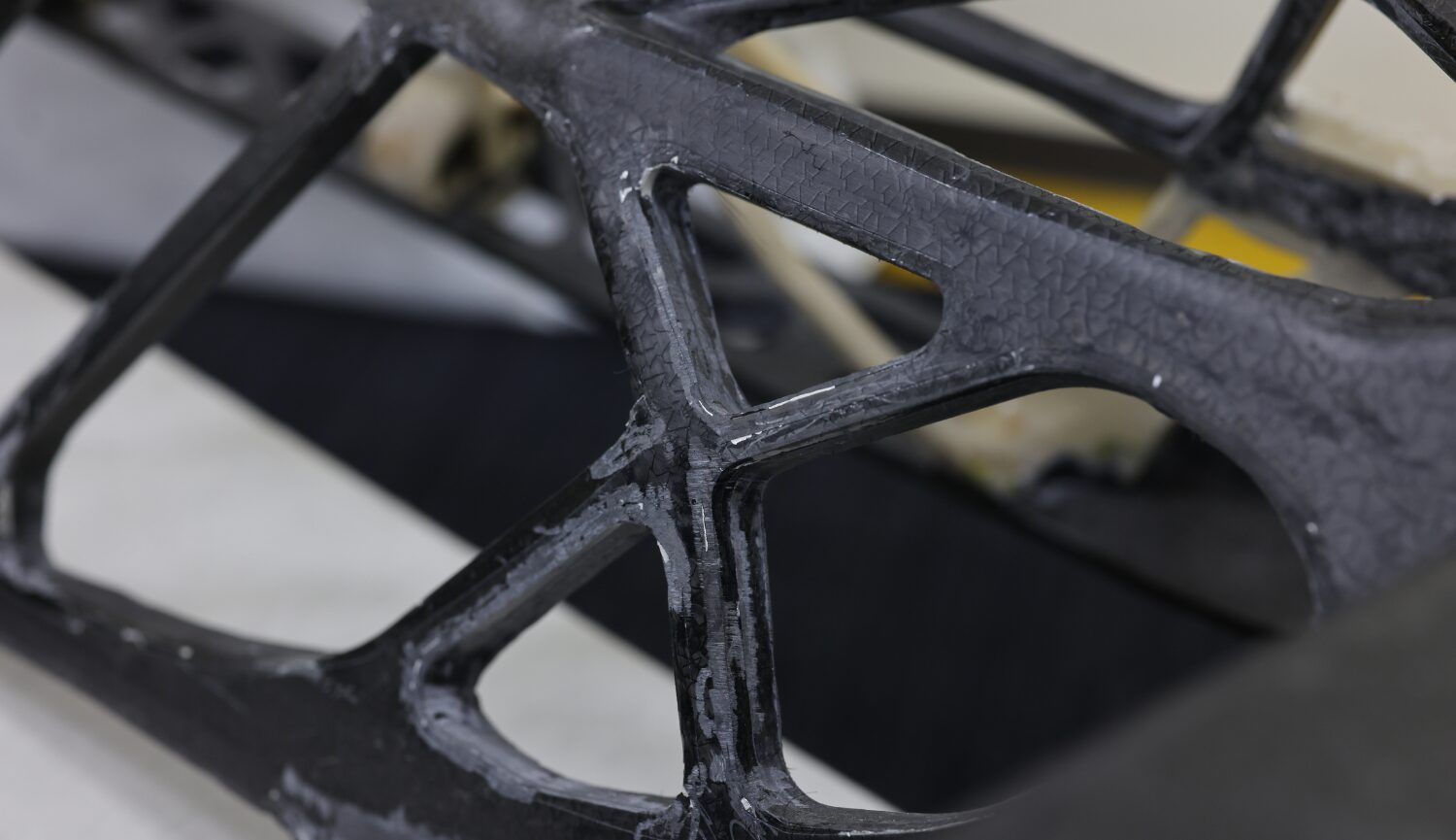
A joint research project with Toyota Motor Corporation is currently in progress to reduce the weight of vehicle wings.
In contrast to the original product, made of aluminum and weighing 425g, the same component made using the TFP process weighed 119g, a 72% reduction in weight, successfully reducing weight while maintaining the same rigidity.
“Reducing vehicle weight enhances fuel efficiency, which in turn lowers CO2 emissions. The TFP process can be applied in such manufacturing. We can proudly say it’s a technology that contributes to carbon neutrality.”
They combined the technologies they had steadily developed and applied them to manufacturing on a larger scale, producing a full-size vehicle monocoque that integrates both CFRP and aluminum.
“It took a lot of time to produce the smaller products we had been working on, so I was surprised when I heard we would be making a 1:1 scale vehicle monocoque. With so many companies involved, we had to meet the demanding role assigned to us.” Reflecting on that period, Ohashi recalls, “The pressure was immense. I remember asking myself, can we really pull this off? “
Manufacturing That Contributes to Carbon Neutrality
In the TFP process, fibers must be precisely oriented to provide strength in the required direction. The orientation is determined by analyzing how forces are applied to each part of the body. A single vehicle monocoque consists of about 70 parts. Ohashi and the TISM development team meticulously sewed CFRP into each individual part with accuracy.
“When sewing fibers (reinforced fibers or carbon fibers), we use undeformed drawings from 3D modeling, which can result in a number of errors in curved surfaces. In addition, the fabric inevitably shrinks when it is embroidered. We had difficulties in creating forms while taking that error into account and adjusting for the difference,” says Ohashi.
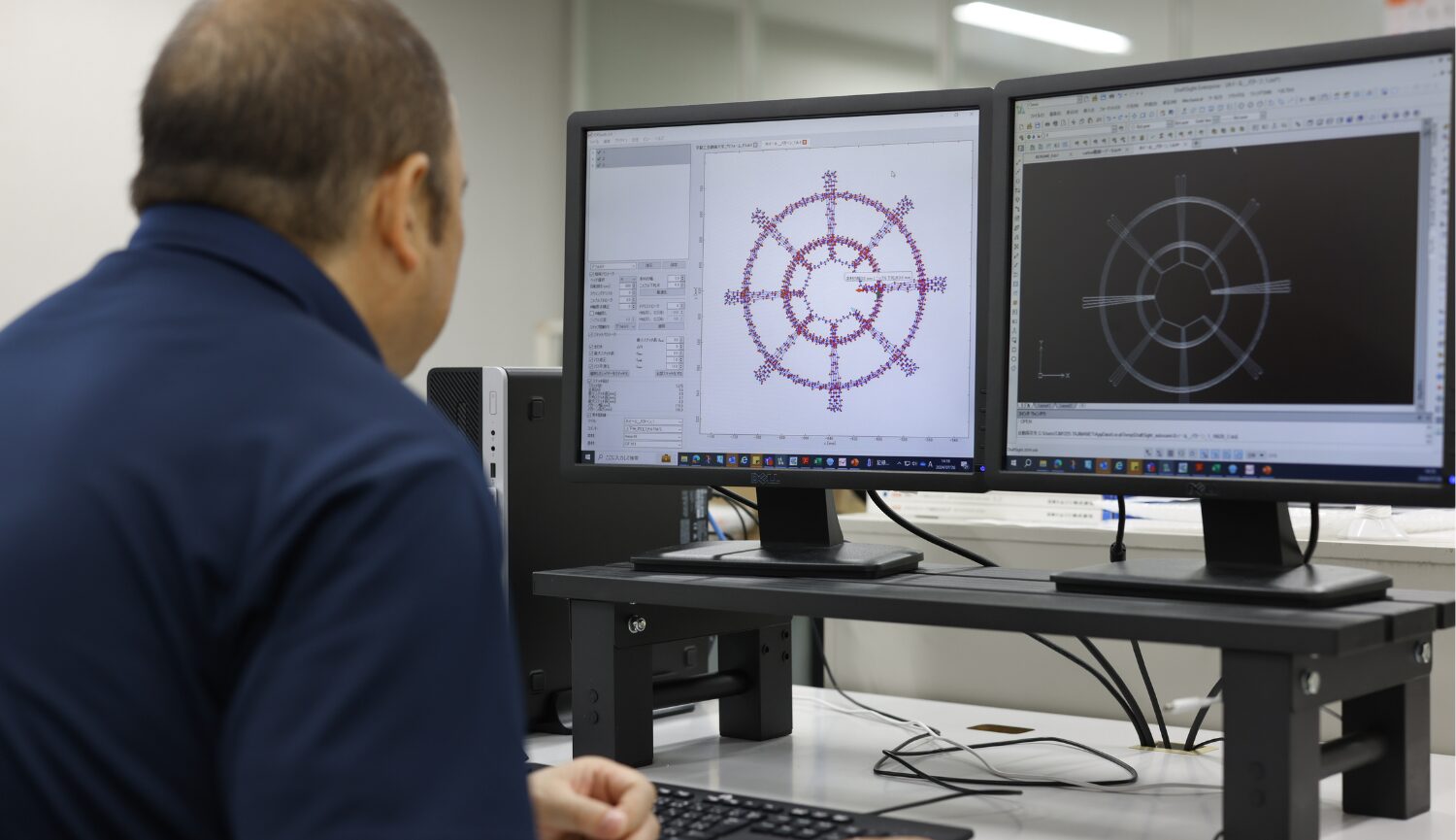
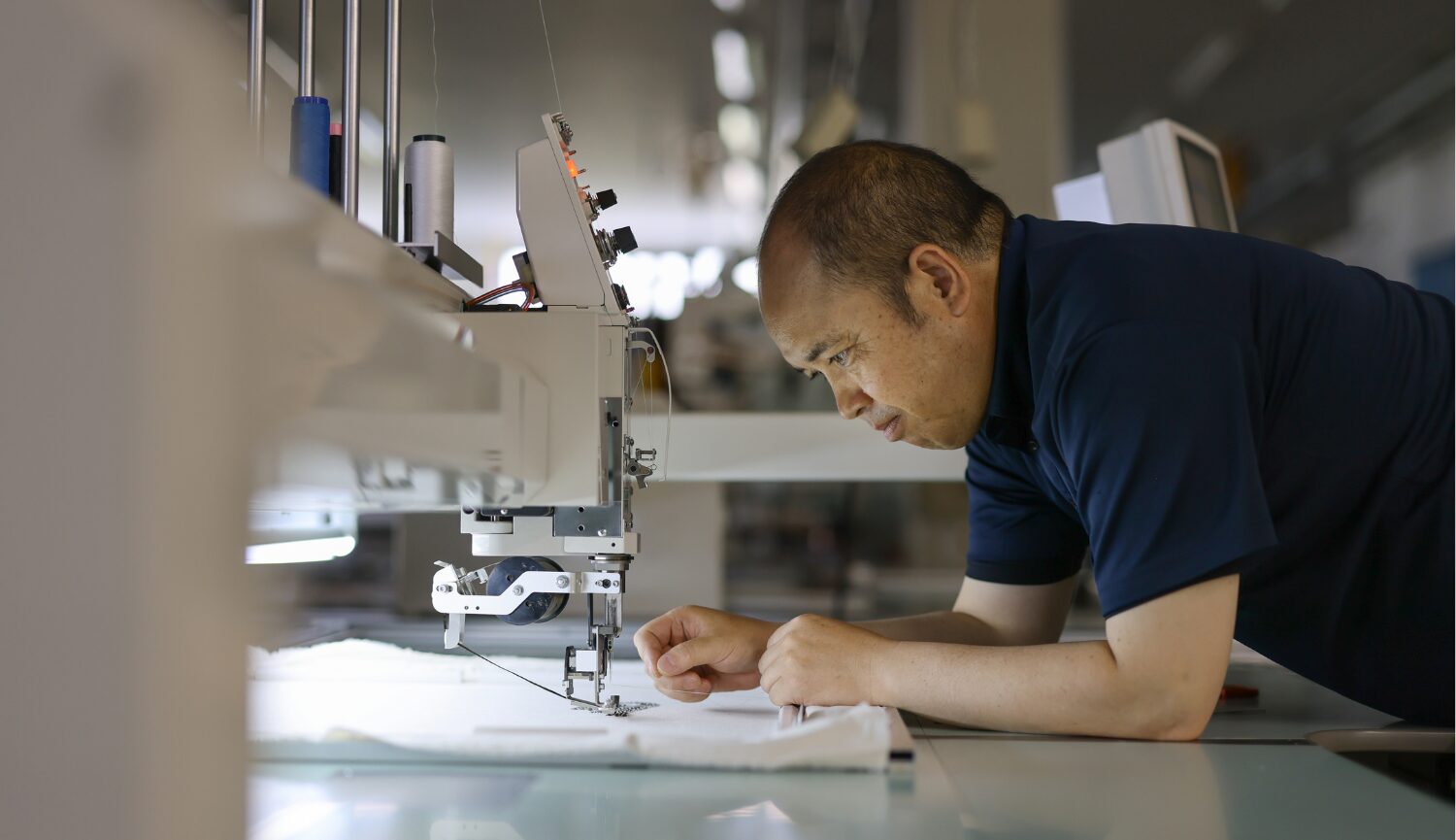
It was a manufacturing challenge no one had ever experienced before. Each of the four companies used their respective strengths in overcoming each problem, and a full-scale monolithic CFRP aluminum monocoque was completed two years after the plan was conceived.Effective use of CFRP has reduced the weight by 15% compared to the 45kg reference design, while also cutting the fiber material scrap rate to 4%. The companies were awarded the JEC Composites Innovation Awards for this manufacturing process, which contributes to carbon neutrality. Applied to the automotive industry, Tajima’s developed embroidery technology has proven successful in addressing a significant social issue.”
Ohashi says, “Many people at our company have worked diligently on developing the TFP process since its inception. I believe this award is the result of that collective effort and experience. I am truly delighted to have received this wonderful recognition.”
Tajima is now exploring additional applications for the TFP process in new fields, such as aircraft and mobility. The team responsible for advancing this technology is accelerating their efforts to contribute to a sustainable society.
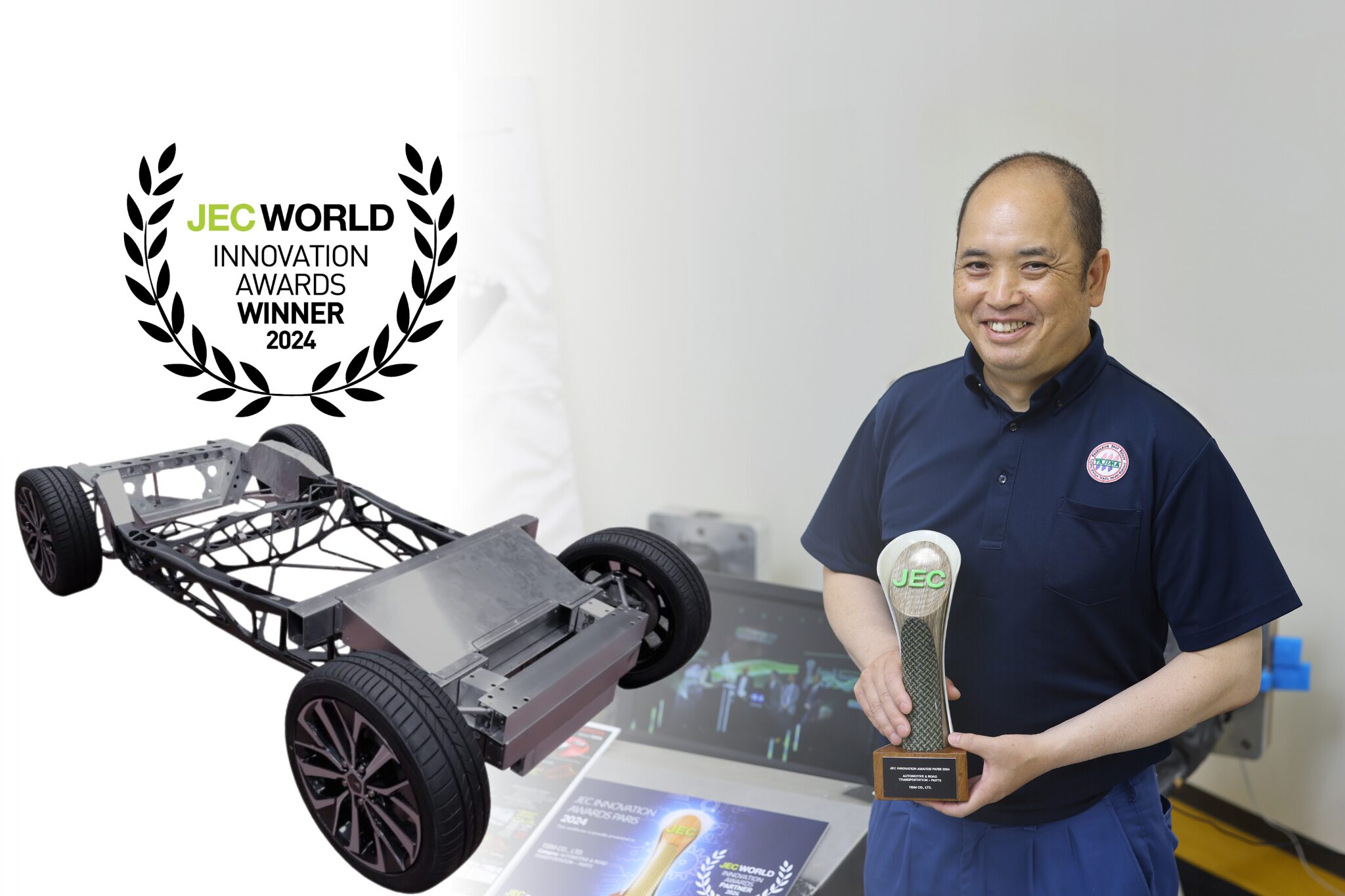
▶「JEC COMPOSITES INNOVATION AWARDS」受賞の プレスリリースはこちら